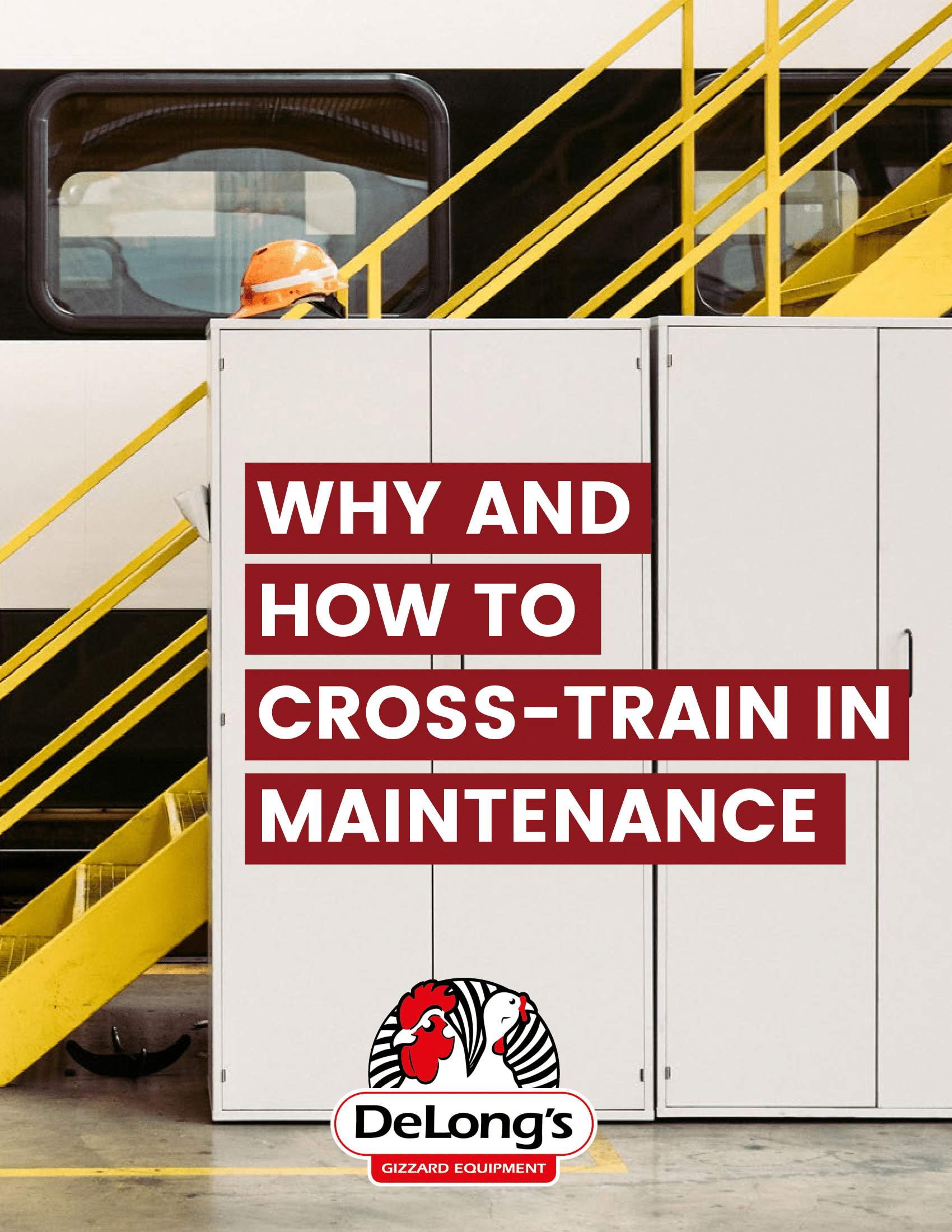
05 Jan Why and How to Cross-Train in Maintenance
Like the equipment housed within, the perfect factory should run like a well-oiled machine, with every part doing its job to contribute toward the end product. A strong factory maximizes efficiency and minimizes turnaround time by leveraging machinery and pushing every piece of equipment to its limit.
Unfortunately, factories and the machines they house carry the same fundamental weakness in that the bigger they get, and the more moving pieces are involved, the more likely something will break. Even the smallest piece can serve a vital function, and plants that fail to properly maintain their equipment can suffer a catastrophic snowball effect. One malfunction leads to systemic failures in the other processes, and a problem that looks small on the surface can have far-reaching consequences.
No matter the size, no plant is unaffected by breakdowns. Obviously, smaller operations that lose a key machine will be crippled, but even a larger company that can keep chugging in spite of a machine breaking down can still see thousands of dollars a minute squandered in the form of lost production opportunity.
Regardless of the full impact, every minute that a machine is broken is a minute that it’s not making the company money. Maintenance and upkeep are therefore a priority, but even a dedicated and knowledgeable team can only work so quickly.
In recent years, many successful plants are shifting the role of maintenance to the floor workers. By cross-training staff in fundamental maintenance best practices, they will be able to communicate more clearly with the maintenance crew and identify the problem area immediately so that it can be resolved as quickly as possible. Better yet, they may be able to prevent a problem from happening in the first place.
In this ebook, we’ll take a look at the threat that machinery breakdowns poses to a poultry plant, how cross-training can alleviate some of the risks, how to implement a cross-training regimen for your staff, and some major issues to be aware of. Through cross-training, your team will gain the tools and know-how to keep your plant running at full speed.
The Cost of Mechanical Failures
The inherent problem with any given machine is that, the larger and more complicated it becomes, the higher the likelihood of one of its pieces breaking. The smallest pieces of the puzzle are easier to overlook, but they’re no less vital to the final product than the big ones.
Problems like loose bolts or dirty grooves may seem inconsequential to the unaware, but that doesn’t change the fact that they can completely wreck a machine. The failure of one operation causes the failure of all its dependent operations, meaning one small small mishap can easily balloon into a huge mess.
Here are some of the ways the mechanical failures can cost you time and money:
Repair or Replacement
The first and most obvious monetary drain is the cost of repairing or replacing the machine. This will vary widely depending on factors like the size of the machine, the availability of spare parts, time constraints, and so on, but the end result still essentially spending money on the machine instead of it making money for you.
Downtime
Depending on the plant, the biggest long-term cost may come in the form of lost opportunities. Bigger plants might be able to make due, but smaller plants can be decimated by the loss of a single, vital machine. The retailers that supply your product will get those products one way or the other, and if your plant can’t make quota, they may move on to a competitor that can.
Health and Safety
While health and safety are paramount regardless of industry, nowhere is it a bigger concern than in food production. If a broken machine leads to an unhealthy or contaminated product, the resulting negative publicity can turn loyal customers into complete strangers overnight. Even after the appropriate steps have been taken to fix the problem, the stain on the company’s reputation may never wash away.
Manpower
No matter the size of the operation, on a long enough timeline, things will break. While this means the maintenance workers will always have a job, preventable breakdowns can stretch an already-busy team even thinner. Worse, young workers with experience in the field are becoming harder and harder to find, leaving some plants with a perpetually-overworked team that never has enough time to fix one problem before a new one rears its head.
Failing to Prepare is Preparing to Fail
Workplace accidents and breakdowns always seem to happen at the worst possible times. But it’s not just your imagination. In fact, in a plant that doesn’t make the most of its maintenance efforts, a breakdown is inevitable.
The longer a piece of equipment has to run and the more strain it’s put under, the higher the likelihood that something breaks. Unfortunately, this means that when deadlines are looming and every machine is running overtime to get it all done, the chances are higher than ever for a breakdown. If one breaks down, the other machines are strained even further to make up for the loss of the first, more breakdowns occur, and the process repeats.
Like the machines themselves, one piece of the plant breaking down can quickly snowball. Therefore, the emphasis for plant owners should shift from repair to prevention, stopping any piece from breaking in the first place so that it can’t have any lasting impact on the plant as a whole.
But the maintenance team can only cover so much ground, and managers are finding it more difficult than ever to find trained and experienced maintenance workers that can fill in the gap. Even if the talent is available, hiring new employees carries its own challenges and considerations.
Instead of taking on more employees, modern poultry plants are instead allocating more responsibility to the ones they have already. The answer lies in cross-training.
How Autonomous Maintenance Can Prevent Major Catastrophe and Build a Positive Workplace
Autonomous Maintenance and Why It Works
Managers looking to get the most out of the maintenance budget need to cross-train floor workers on basic maintenance and upkeep of the machines they oversee by adopting the concept of autonomous maintenance.
Autonomous maintenance shifts the focus of the maintenance team from fixing problems as they arise to preventing them from happening in the first place. Under the autonomous maintenance model, individual floor workers at the plant assume responsibility for the general upkeep of the machines they oversee.
Instead of either waiting for scheduled maintenance or running his or her machine until it breaks and then calling the maintenance team to fix it, each individual worker is trained in basic maintenance protocols that boost the machine’s lifespan. Workers are trained on all the specifics of the machine, and take it upon themselves to clean it, lubricate it, and inspect it for things like damages, loose bolts, and common defects.
With floor workers assuming the responsibility of basic repairs and general upkeep, the maintenance team is now free to focus on preventive steps and improvements that can keep each machine running longer and more safely. This in turn allows them to overcome the otherwise unpreventable downtime that would occur during peak periods. When repairs are necessary, preventive maintenance assures that they’re much less costly and result in much less downtime.
In addition, the more people that know the common problems to look out for, the higher the likelihood that they’ll be caught before disaster can strike. The maintenance team will still be there to solve big problems, but will see a smaller overall workload. The individual worker may not be able to solve the problem, but he or she will be able to pass it along to a dedicated maintenance team member who can.
Building Bridges
In many plants, one of the major problems facing the maintenance team is the relationship it has with the production team. All too often, the production team gets the credit when things go right while maintenance gets the blame when things go wrong.
Maintenance finds itself in a lose-lose situation. Beyond the animosity that can develop from this type of situation, it can also lead to a lot more finger pointing when teams blame each other for setbacks instead of working together to find solutions, leading overall workplace morale to suffer.
In addition to plant efficiency, one of the key benefits of autonomous maintenance is that it lays the foundation for a natural partnership between the maintenance and production teams. Through autonomous maintenance, the production team bears part of the responsibility for machinery malfunctions and setbacks, while the maintenance team’s proactive and preventive steps serve as proof that they were just as instrumental in success.
Additionally, autonomous maintenance gives the individual operator a sense of ownership. Instead of simply running their machine until it breaks, they are in charge of taking care of it. Because the operator knows the individual parts of the machine better, safety is improved, and because he or she can better illustrate to the maintenance team exactly what’s broken, downtime is decreased.
When the both teams share accountability both for success and for failure, they are motivated to come together and prevent problems before they happen so that success naturally follows.
Maintenance Issues All Staff
Should Know How to Handle
Once you’ve decided to implement a cross-training regimen at your plant so that you can start using autonomous maintenance, it’s then time to decide what specific areas workers should be cross-trained in.
While every plant will have its own specific needs, here are some great starting points:
Dirt and Grime
Over time, dirt can easily collect in the grooves, sockets, and other nooks and crannies of a machine, causing it to lose efficiency. Over time, if enough dirt is allowed to build up, it can shut down a machine completely when essential processes become impossible due to dirt and grime buildup, to say nothing of the health hazards that dirt can present.
While most plants will already place a heavy stress on the importance of clean equipment, an effective autonomous maintenance regimen will teach in-depth strategies that every worker should know to clean any piece of machinery they interact with. In particular, make sure to emphasize out-of-the-way and hard-to-reach areas that might go unnoticed to the unaware.
Proper cleaning of a machine comes with the added benefit of making other problem areas more easily visible.
Contamination
Cleaning dirt is great, but stopping it from getting inside the machine in the first place is even better. After all, prevention is one of the key concepts of cross-training and autonomous maintenance, and removing or minimizing the sources of contamination can reduce the need for repetitive cleaning.
Have all workers be on the lookout for areas where dirt and contaminants might be getting into the plant. Employees should be on the lookout for cracks in the walls, leaking vents, unsecured windows, and the like, and report any defects to the dedicated maintenance crew to repair.
Loose Nuts and Bolts
As dirt can gradually build up, nuts and bolts can loosen over time, leading to potentially catastrophic breakdowns and health risks.
When cross-training workers, make sure that everyone goes over their machines thoroughly to ensure everything is tight. Instruct workers on the warnings signs of a machine with loose nuts and bolts, and encourage them to take the initiative to keep things running smoothly.
Lubrication
While removing dirt and tightening loose bolts is essential to giving each machine the longest lifespan possible, they won’t be running at maximum efficiency if the pieces aren’t well-lubricated.
Train employees on the different moving parts of their machines, and on proper lubrication procedures. In particular, ensure that employees know the proper amounts of lubricant to use to reach the best effect on each piece, and how often the machine as a whole should be lubricated.
Training Your Poultry Plant Employees & Developing Maintenance Issue Report Protocol
Now that you know some of the importance of employee cross-training and some of the points to emphasize, let’s look at how you can start training your workers to build a better, more autonomous plant.
Employee Training Best Practices:
- Incorporate visual, auditory, and tactile learning processes. Different people learn in different ways. Some learn by reading PowerPoints and informative printouts, others by listening to a lecture, and others by getting to physically touch and hold the equipment and machinery. For the best results, try to incorporate all three learning styles as often as possible, and don’t be afraid to present the same information in multiple ways if necessary.
- Use real case studies. Even if a worker can understand the fundamental principle behind an operation, nothing puts it in perspective like having a real-world example. Don’t stick to positive examples: sometimes, it can be just as important to learn what not to do and some common mistakes that others have made in the past.
- Keep a regular training schedule. People are creatures of habit, and tend to learn better if they can stick to a routine. By scheduling regular training sessions at the start of every month or every quarter, you’ll find your employees will be much more receptive to learning. Holding training sessions at regular intervals can also provide an opportunity to give each employee one-on-one feedback on their progress from last month.
- Vary training topics and formatting when possible. While employees benefit from a regular schedule, if they know that they’re just going to see the same presentation from last month, they’ll immediately turn-off. For the best results, try to vary the topics covered during training sessions, or to switch the way that information is presented. For example, you might provide two different solutions to the same problem, or have workers approach the problem from a different direction.
- Train maintenance and operations workers simultaneously. This is especially important for autonomous maintenance, and will help remove any communication gaps between the two teams. The operators can ask the maintenance team directly about different protocols, and the maintenance team will be given an opportunity to explain first-hand why different procedures are in place and give examples from their own personal experiences. This will also serve to build personal relationships between the members on both teams and grow the sense of unity at the plant.
Training is only part of the battle. After it’s done, ensure that workers are given their own tools and equipment to start maintaining their machines, and conduct regular maintenance reports to track their progress.
Maintenance Reports
Reports are a vital part of continued autonomous maintenance success. After all, how can you know what needs improvement if you don’t know where you stand?
Another key reason why maintenance reports are so important is that it builds accountability on the part of both the maintenance and operations teams. When every potential problem has been duly reported and filed, finger-pointing between teams becomes less of an issue because the proper protocols should already be in place to decide who was responsible.
To get the best, most comprehensive reports possible, it’s essential to make the report as comprehensive as possible. First, it’s important to categorize the types of defects and problems you’re encountering, such as machine downtime, defective products, slow production speed, etc.
Once you’ve found a good way to categorize the problems your plant faces, find out which team should be responsible for which defect. This is an essential aspect, because it removes any of the he-said/she-said problems you might otherwise face. When every fault has to be explicitly written down and employee roles clearly defined, it removes any ambiguity in what the next steps should be and who should be the one to take them.
Keep in mind that every report is a potential new area for training. If you’re seeing a lot of reports that cover the same topic, it might be time to dedicate a training session to it and ensure everyone knows what to do when the problem arises in the future.
Over time, as your workers grow better at identifying exactly what problems are occurring and learning for themselves the best way to solve them, you’ll find your plant seeing more autonomous maintenance, less downtime, and a more streamlined production process.
Now you know some great ways to train your employees to make the most of your plant’s processes. But even a plant with the best maintenance practices in place still needs equipment to make it run.
At Delong’s, we excel in creating, repairing, and replacing the machinery and rollers that make poultry plants thrive. Request a consultation today and find out more about solutions we can provide your plant.
SOURCES:
- http://www.meatingplace.com/Industry/ TechnicalArticles/Details/53635
- http://www.meatpoultry.com/Writers/Other-Contributors/ Partnering-pays-off.aspx?cck=1
- https://www.epa.gov/lean/lean-thinking-and-methodstpm
- https://www.epa.gov/lean/lean-thinking-and-methodstpm
- http://www.meatpoultry.com/Writers/Other-Contributors/ Confidence-and-concerns.aspx
- http://leanmanufacturingtools.org/425/preventivemaintenance/
- http://leanmanufacturingtools.org/427/predictivemaintenance/
- http://leanmanufacturingtools.org/438/autonomousmaintenance/
- http://www.meatpoultry.com/Writers/Other-Contributors/ Confidence-and-concerns.aspx