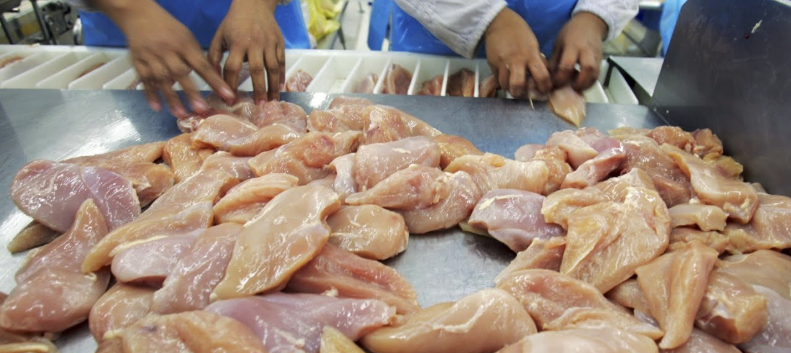
02 Mar Ways to Maximize Yield Throughout Poultry Processing
When it comes to reducing costs at processing plants, look no further than to your yield. Maximizing your yield can be the difference between making a large profit or suffering a loss.
Naturally, increased yield drives down the cost of a product and increases volume without additional costs.
When birds are counted at the poultry processing plant, discrepancies between the quantity of birds arriving from the poultry farm and those which were actually processed is determined.
Because processing plants sell pounds of poultry meat, counting is simply not enough to determine yield. It is imperative that you have equipment and methodologies in place that can take measurements at different intervals along the processing line.
Here’s a look at how to maximize yield throughout the duration of the processing!
Ways To Maximize Yield
Minimize Holding Times and Provide Proper Holding Areas
By providing proper holding areas for birds who are coming to the processing plant, you can work to reduce the stress on the birds and ensure their welfare until the time for slaughter. Many birds who are dead-on-arrival have endured extreme thermal stress from their time in the transportation truck and their wait in the holding area.
By providing holding areas that maintain controlled temperatures, lighting, and ventilation, birds will be kept calm, reducing stress. A holding shed with high speed fans that use water will also help to keep the birds comfortable until they meet their demise.
Provide Efficient Unloading and Proper Hanging Operations
This could perhaps be one of the most important steps in maximizing yield. Unloading and hanging helps provide for a more efficient slaughter and if done incorrectly could cause yield loss throughout the entire process.
Make sure you always have a full supply of birds in the hanging area to keep the line as full as possible. When there are empty shackles, misfeeding can happen and timing of the process can be off. While maintaining a full line, be sure Birds are never thrown on top of each other, as they could be smothered. Again, decreasing yield. Be sure to train employees on the correct way to do this, so as not to damage any part of the bird.
In setting up a proper hanging area, keep these things in mind:
- Dark area with no UV light
- Make sure shackles are at the right height
- Ensure shackles match the bird’s size, so as not to damage the feet throughout the process.
Complete the Slaughter with Minimal Damage
At this stage in the process, the birds are stunned and slaughtered to remove blood and humanely kill the bird. The key to avoiding a drop in yield at this step is to avoid damage or downgrade to the bird.
Once the bird has been stunned with an electrical shock, they proceed to the automatic kill machine. It is here that you want to make sure the cut is clean and severs the carotid artery, jugular vein, and windpipe. The average time it takes for the bird to “bleed” out when this method is employed is around 90 seconds.
If the bird is not cut correctly and the bleeding time is too short, loss will be endured at later stages of the process.
Ensure Proper Scalding Temperature and Picking Power
When it comes time for scalding and picking, there are small details that could make the difference between a huge yield loss or gain.
Make sure your scalder is kept at the right temperature and maintained a good agitation to wet the feathers thoroughly. If the temperature is too hot, you will risk the chance of overscalding which can actually partially cook and discolor the meat.
As for the picking process, it is imperative to remember to set the picker to the largest birds in the flock being processed.