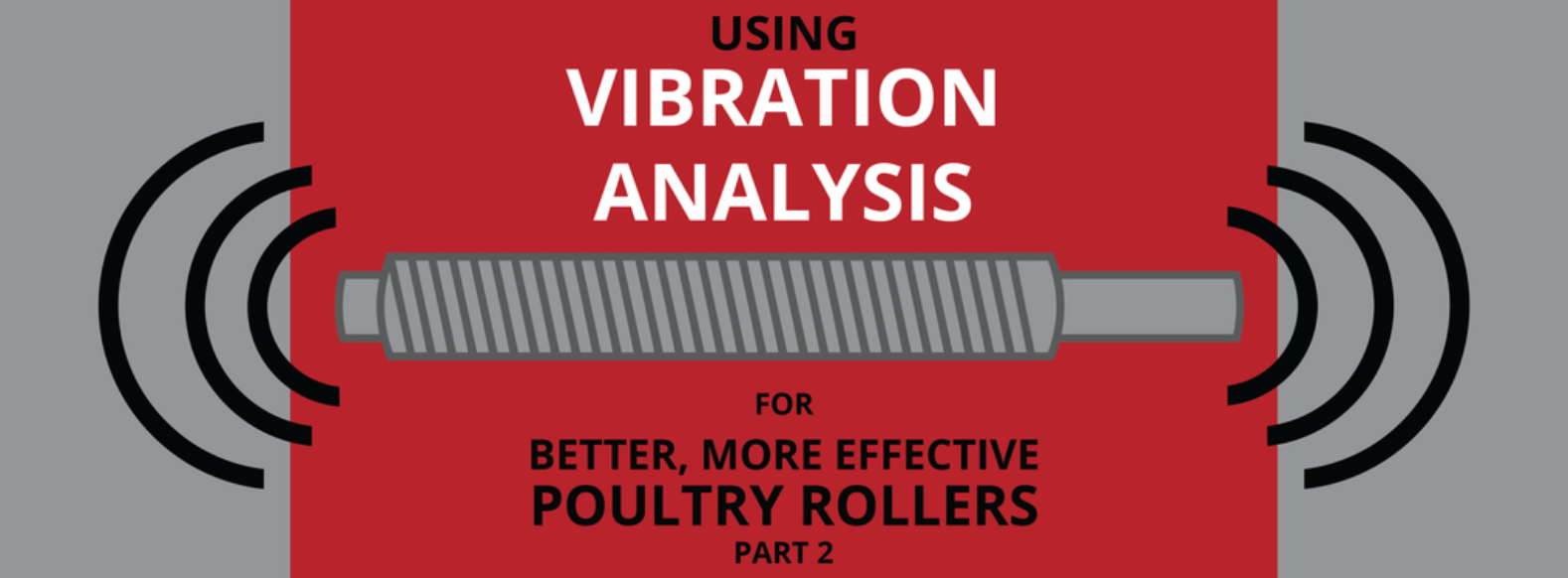
07 Nov Using Vibration Analysis for Better, More Effective Poultry Rollers, Part 2
Adoption and expansion of vibration analysis technology is one of the fastest-growing trends in food production, and with good reason.
In our previous entry, we explained what vibration analysis technology is, how it works, and the advances that have been made as the technology continues to improve. In this section, we’ll dig deeper into the many benefits vibration analysis can bring to any poultry plant, and how managers can use this information to get better, longer lasting poultry rollers for their plants.
The Benefits Vibration Analysis Brings
While there potential applications vibration analysis can bring to a plant are endless, four key benefits make it particularly attractive to production facilities:
1. Non-Intrusive Monitoring
Vibration analysis allows for effective, non-intrusive monitoring for any machine at any time, from startup to shutdown and everywhere in-between. Downed machines can be quickly diagnosed to determine the cause, while machines still on the line can be analyzed for any potential problems without having to be taken off the line or disassembled.
This component can also be applied in areas beyond maintenance and repair. For instance, when deciding on the best decision for a replacement machine, managers can run two machines from different manufactures and monitor and use the results to determine if specific design differences correlate to increased – or decreased – overall performance.
For smaller plants with limited budgets that can’t afford to take a key machine off the line during critical periods, unobtrusive monitoring allows managers to see exactly how long they can keep the machine on the line before they risk a breakdown. With deadlines looming, this can be the deciding factor in getting quotas filled.
2. Problem Recognition
Using vibration analysis, maintenance personnel can not only determine that a problem exists, but also the type of problem present. Different problems require different solutions, so one benefit for maintenance personnel is the ability to identify if the problem stems from misalignment, defective bearings, loose parts, or something else, and respond accordingly.
If equipment is being pushed beyond design specifications, such as operating at higher speeds, loads, or temperatures than intended, the problem can be quickly understood and properly rectified.
Modern analysis systems can also determine if misalignment was due to machine error or improper repair and maintenance practices. Improper bearing installation and replacement, inaccurate shaft alignment, or imprecise rotor balancing can be ascertained early and addressed appropriately. If the same recurring problems continue to spring up, managers can use these insights to revise their practices and educate workers on what’s going wrong.
3. Customization:
Machine monitoring is widely customizable based on the needs of the plant. Managers incorporating vibration analysis tech can tailor the system to fit the plant’s existing processes and maintenance schedule for a seamless integration.
Larger plants might want constant surveillance on every piece of equipment, while smaller or budget-restrained plants might only have constant monitoring for the most vital machines and have the rest analyzed on a weekly, monthly, or quarterly basis.
4. Accident Prevention
Of all the potential benefits vibration analysis can bring to a plant, undoubtedly the greatest is the ability to prevent accidents before they happen.
By analyzing trends in vibration levels across any given machine, workers can project the machine’s condition into the foreseeable future. This allows them schedule necessary maintenance at times when the machine was already scheduled to be down, meaning that short-term productivity never has to take a dip in exchange for long-term effectiveness.
Vibration analysis allows maintenance personnel to shift their focus from putting out fires to ensuring they never have the opportunity to occur in the first place. On the front end, this means better installation quality and higher precision in initial alignment and balancing. Over time, it means lower average equipment vibration levels throughout the entire plant.
Vibration Analysis For Poultry Rollers
While vibration analysis technology can be applied to a number of operations throughout any production plant – such as steam and gas turbines, pumps, motors, compressors, machine tools, and gearboxes – it serves a particularly vital role in poultry plants in regard to poultry peeling rollers.
A recurring problem for many plant owners is not knowing when to refurbish rollers and when to replace them outright. Of course, sometimes the problem stems from dirt or grime build-up, and can be alleviated just using proper cleaning procedures. Likewise, analysis can indicate that a roller has simply fallen out of alignment, saving you the cost of replacement if you can simply set it back correctly in place
Vibration analysis takes out the guesswork so that managers can make the best, most informed decision on how to proceed. While the technology is not without its challenges, with the proper education and training, it can mean all the difference for poultry production managers looking for higher yields and a more productive plant.
Incorporating vibration analysis is just one of many steps poultry plants can take to get the most out of their rollers. For more tips and strategies you can use to push your poultry rollers further, check out our free informative guide, The Lifecycle of a Poultry Roller, and start getting better yields at your plant today!