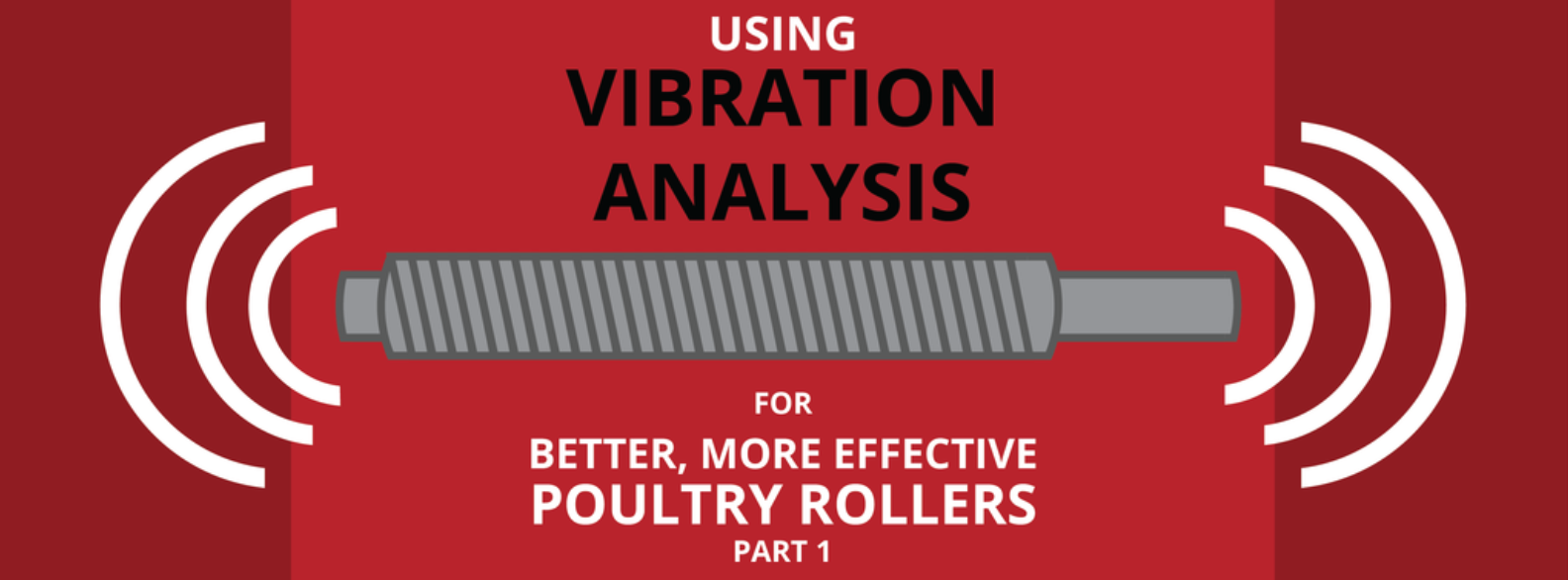
31 Oct Using Vibration Analysis for Better, More Effective Poultry Rollers, Part 1
In the world of poultry production, downtime can be a death sentence. Depending on the size of the operation, a machine that has to be taken off the line for as little as an hour can result in thousands of dollars in lost profits.
If that wasn’t bad enough, these problems can snowball during peak production periods throughout the year. With deadlines looming and quotas to fill, many machines are already running overtime; when one breaks, the others have to work even harder to make up the difference – making another machine breakdown even more likely.
With so much at stake, managers are always on the lookout for strategies to reduce downtime in their plants. While there are a number of great practices any plant can take to keep downtime to a minimum, a growing number of plants are turning toward new and innovative technologies to keep everything running smoothly.
One such solution lies in the growing field of vibration analysis technology. In this blog, we’ll take a deeper look into vibration analysis, how it works, and how the technology continues to improve in effectiveness.
What Is Vibration Analysis?
In any complex machine, individual parts will move back and forth from a position of rest during operation. Some vibration is unavoidable, but excess movement can create unwanted byproducts, such as excess heat and friction, that can cripple a machine’s overall effectiveness and eventually cause a complete breakdown.
Enter vibration analysis.
With this technology at their disposal, plant managers gain the ability to monitor and record the vibration levels of any machine at their plant. The data obtained can then be analyzed and used to determine the operating and mechanical condition of any piece of equipment and identify potential problem areas in the machine before catastrophe strikes.
Should something break, the repair team can use vibration analysis to trace the root of the problem and repair it more quickly than with traditional means. Better yet, common problems that can cut any machine’s life short – such as defective bearings, mechanical looseness, worn or broken gears, and so on – can be quickly identified and rectified before they can fester and negatively impact the machine’s effectiveness.
How It Works
Most vibration analysis systems have three core components:
- Transducer: Also called the “signal pickup,” detects vibrations
- Signal analyzer – receives and interprets data received from the transducer
- Computer – uses analysis software to present information in a legible and actionable manner to the operator
These components can then be configured to form a continuous online system, a periodic analysis system using portable equipment, or a multiplexed system that samples a series of transducers at predetermined time intervals.
Using the measurements of vibration amplitudes in a given machine, managers can gain valuable insights about the machine’s overall fortitude, including the accuracy of shaft alignment and balance, the condition of bearings and gears, the effect on the machine stemming from resonance from housings, piping, and other structures, and more.
How Vibration Analysis Has Improved
While it has seen widespread adoption in recent years, vibration analysis as a tool has existed for some time. However, as the technology continues to improve, the scope of analysis – and the level of insights managers can gleam – has only increased with time.
In the past, vibration analysis was a fairly complex process, requiring the user to dial an instrument through the full spectrum of identifiable frequencies in order to get an accurate reading. The operator then had to manually compare the peak frequencies with the operating speed, which could be cross-referenced to determine a number of possible causes.
As with virtually every other industry, automation has gone a great way to make vibration analysis a simpler and more streamlined process than before. Modern operators can monitor the full vibration spectrum of three axes simultaneously, giving them a snapshot of the entire machine’s vibration levels that can then be dissected to identify individual problems.
This information is then compiled into a database that can be accessed by anyone working on the machine to find out exactly what’s wrong with a machine, sometimes before anyone knew that a problem existed in the first place.
As vibration analysis technology continues to improve, so do the benefits they bring to the poultry production industry – poultry rollers in particular. For an in-depth exploration of the benefits vibration technology can provide, and how managers can use them to get better yields and higher efficiency out of their rollers, continue to Part 2.
However, vibration analysis is only one component of finding the best poultry rollers for your plant. If you’re looking for more information on giving poultry rollers at your plant a longer, more productive lifespan, download our free informative guide, The Lifecycle of a Poultry Roller, for all the best tips and strategies to help you make the best decision for your plant.