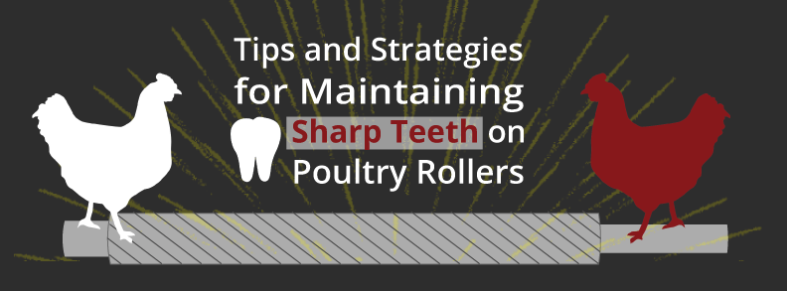
05 Dec Tips and Strategies for Maintaining Sharp Teeth on Poultry Rollers
The teeth on any given roller are arguably the most important component to consider when trying to maximize yields. Dull teeth can cause mis-cuts and damage that could destroy usable product, while excellent teeth can help managers make perfect cuts that harness more usable material and leave more of the bird fit for consumption.
In this blog, we’ll explain why sharp teeth are so important, what they’re up against, and what you can do to help them cut better and last longer.
The Importance Of Sharp Teeth
Poultry peeling rollers have three principle parts: the shaft, the peel, and the blocks that keep the rollers in place. As the name implies, the actual peeling action of the roller is performed by the peel, which is lined with sharp teeth that tear into skin, gizzards, and membranes so that the bird can be further processed until it’s ready for consumption.
The condition of the roller’s teeth is one of the most important factors affecting yield size in poultry production. Poor teeth can easily lead to mis-cuts and lost product, while sharp and effective teeth can allow managers to get the best return possible for their investment.
Unfortunately, poultry roller teeth are subject to a considerable amount of wear-and-tear as part of their function. Beyond natural rusting, weathering, and breakdown over time, the teeth also bear direct damage from the birds they eviscerate.
Birds don’t have stomach enzymes that naturally break down food the way humans do; instead, they have to swallow hard objects, usually stones, and store them in their gizzard. The gizzard’s thick muscular walls then move those stones and cause them to grind up food particles, which then pass on to the bird’s true stomach.
However, while stones are the most common objects most peelers have to contend with, they are far from the only example. Chickens and turkeys will eat almost anything they come across, so it’s not unheard of to have peelers get damaged as they try to tear into other metal objects like coins, screws, and even bullets and brass bullet casings.
With so much wear and tear happening to a part that plays such a vital role, it stands to reason that plant managers are always on the hunt for ways to help their roller teeth last longer and perform better.
Getting Better Roller Teeth
When it comes to getting better teeth, there are aspects key things to keep in mind: preserving existing rollers to last longer, having existing rollers re-cut for a better function, and finding more effective replacement rollers.
Maintenance
Of course, just like the rest of the roller, the best way to keep poultry peeler teeth sharp is just by staying on top of regular cleaning and maintenance. Just like any other piece of your equipment, no roller lasts forever, but having a maintenance schedule in place for rollers can go a long way in giving them the longest lifespan possible.
Rollers should be cleaned every night during the sanitation shift, sprayed down with pressurized water to ensure that nothing is missed and that every part of the roller gets an even treatment. In addition to regular maintenance practices, don’t forget to check your rollers’ blocks and bushings to ensure they’re snug and allow the roller to spin effectively.
Likewise, it pays to invest in some preventive maintenance practices. In recent years, developments such as vibration analysis and thermal imaging have made the process of finding and eliminating problems in rollers faster and easier than ever before. These sorts of advances will also help you gauge how long a roller can be kept on the floor before it needs to be replaced.
Refurbishment
Getting rollers professionally refurbished is another way to squeeze a much efficiency out of them as possible. They’ll still need to be replaced eventually, but refurbishing can take them to like-new quality, which includes having their teeth sharpened to allow them to get yields on par with what they produced when they were first put on the line.
Of course, sharper teeth are just one of the reasons why refurbishing your plant’s rollers can be a cost-effective means of boosting plant productivity. For money-conscious plant managers, roller refurbishment is a great way to get like-new yields for about a third of the cost of replacement. Just keep in mind that not every roller can be refurbished.
Buying New
Maintenance and refurbishment can go a long way in getting better returns out of your rollers, but unfortunately the effectiveness these steps bring won’t last forever. Rollers are always breaking down over time, but the better constructed they are at the outset the longer they’ll last and the higher yields they’ll bring.
For this reason, one of the biggest components of achieving better teeth in your plant’s rollers is to simply start buying better quality rollers. Refurbish and maintain them, but take care to understand the factors influencing them and the warning signs indicating that a roller is due for replacement – and don’t be afraid to take a roller off the line and replace it if it has lost efficiency.
In recent years, many poultry producers have begun implementing custom rollers in their plants. Custom roller creation utilizes a step-by-step process that incorporates classic techniques with modern advances in order to create rollers that outlast their factory original counterparts while simultaneously boosting per-bird yield.
Sharp teeth are just one of many important aspects that determine a poultry peeling roller’s efficiency. For more information about how to get more out of your rollers, download our free informative guide, The Lifecycle of a Poultry Peeling Roller, and start getting better yields at your plant today!