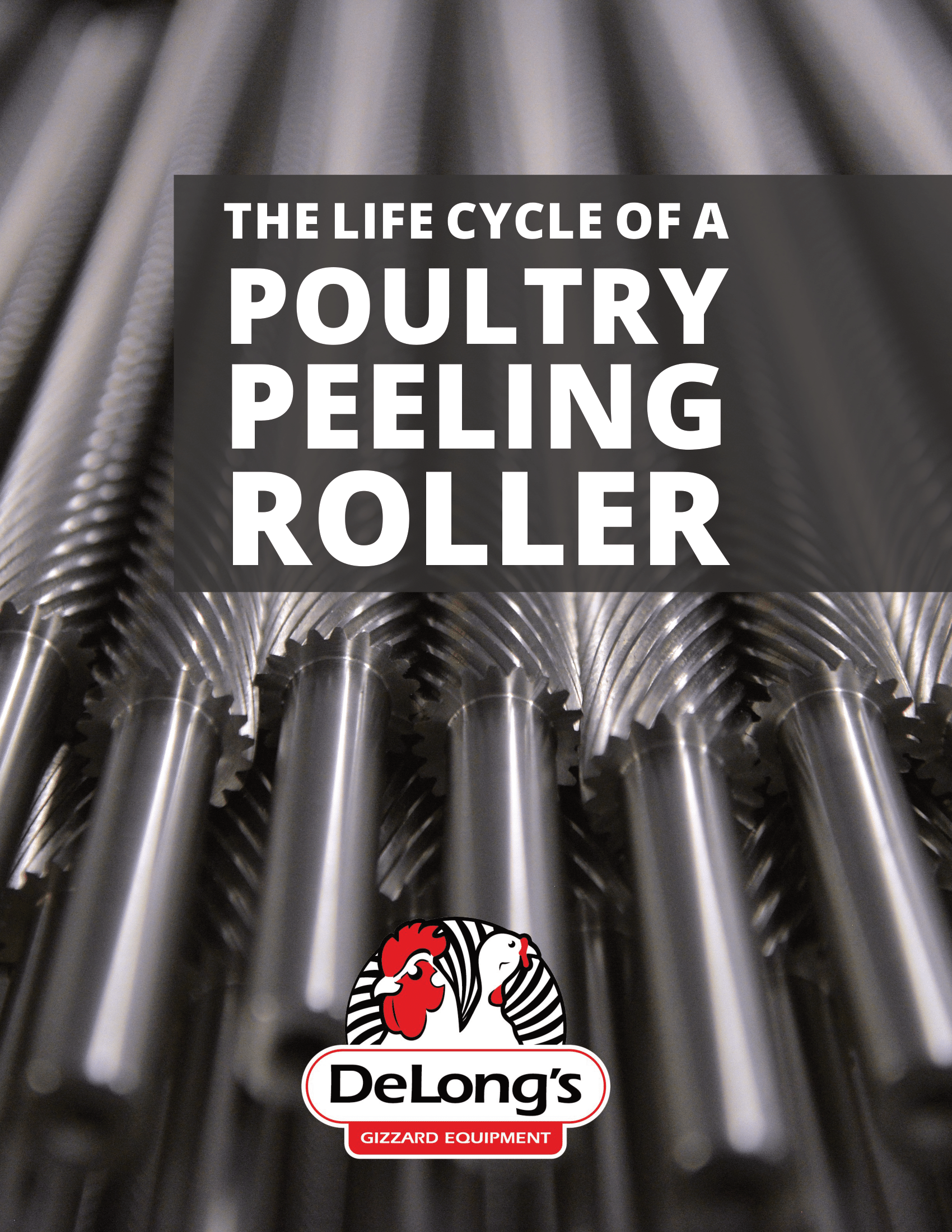
05 Jan The Lifecycle of a Poultry Peeling Roller
INTRODUCTION
Managers are always on the lookout for machinery that lasts longer, performs better, and produces higher overall yield. If you want to maintain a high yield at your plant, you have to understand where your poultry rollers fit into the overall equation. Worn, low-quality poultry rollers lead to wasted raw materials and lost profits, so knowing when and why to repair, refurbish, or replace a roller is essential. Leaving a roller in rotation too long can lead to damage and lower yield through over-processing; on the other hand, cleaning, maintaining, and specializing your plant’s rollers can cause yields to increase dramatically. In this informative guide, we’ll take a deep look at how rollers play into a poultry production plant’s overall process, the different types of rollers in play, and what factors affect them. Finally, we’ll discuss how and why to keep rollers cleaned and maintained, when it’s appropriate to refurbish a roller, and when it’s time to start looking for a replacement.
ROLLER TYPES
In the past, the part removal and evisceration process was 100% manual. In modern plants, the process can be semi- or fully automated, but the need for effective rollers remains. Modern rollers typically come in one of four categories: gizzard peeling, gizzard harvesting, breast cleaning, and neck & thigh skinning. While all the rollers in a given category will perform the same basic function, rollers will vary in size based on four dimensions:
PEEL LENGTH
Length of the peel, the part that performs the roller’s key function of removing skin, membranes, fat, etc.
PEEL DIAMETER
Diameter of the peel, necessary to find accurate end blocks.
SHAFT LENGTH
Length of the shaft, the rod protruding off of the peel used to drive it.
SHAFT DIAMETER
Diameter of the shaft, necessary to find accurate shaft bushings.
Rollers can vary wildly in size based on the machine they are used in. Below is a chart depicting each type of roller, its specific function, and the range of sizes for the roller.
A. Manual Gizzard Peeling Rollers
Used for removing membranes and fat from poultry gizzards. Dimensions will vary.
B. Breast Cleaning Rollers
Used for removing membranes and skin from poultry breasts. Dimensions will vary.
C. Automatic Gizzard Peeling Rollers
Used for removing any membranes or skins present. These rollers are designed that the operator will never touch the rollers. Dimensions will vary.
D. Neck & Thigh Skinning Rollers
Used to safely and effectively skin poultry necks and thighs. Dimensions will vary.
FACTORS THAT AFFECT PERFORMANCE
AGE
The ultimate deciding factor affecting a roller’s performance is its age. No matter how well-maintained, every piece of equipment at a poultry plant will eventually break down once enough time has passed, and rollers are no different. The industry standard lifespan for rollers is 6-8 weeks, with overall yield dropping by as much as 10% every week the roller is kept in use past this period. While proper cleaning and maintenance procedures can extend a roller’s life considerably, no roller lasts forever. To keep yields high, you’ll have to change your plant’s rollers on a regular basis.
SHAFT CONDITION
The shaft on the roller should also be taken into account. Like the teeth, the shaft itself will become worn down over time which will have a detrimental effect on the roller’s ability to spin effectively. This will cause possible yield loss as the rollers hit each other due to the extra room they will pinch and bit the product.
TEETH SHARPNESS
A more-specific example of how the age of a roller affects its productivity comes from the sharpness of its teeth. Over time, a roller’s teeth will get worn down and dull, drastically degrading its ability to remove a bird’s skin and membranes effectively.
MATERIAL
Poultry rollers generally come in one of two material compositions: tool steel or stainless steel. While there isn’t a discernable difference in lifespan between the two types, tool steel rollers are cheaper but susceptible to rust, while stainless steel rollers are rust-proof but on average $38 more expensive per pair.
While stainless steel rollers are more prevalent in plants in the United States, the USDA has the final word about which materials can be used in which plants.
AUTOMATIC VS MANUAL
Whether your plant operates using manual or automatic rollers will also have an impact on its overall productivity. Like most industries, poultry production becomes more and more automated as technology improves; however, automatic rollers have yet to fully replace their manual counterparts, and there are pros and cons associated with each.
Because they work at a steady pace without fluctuations, automatic rollers produce a more predictable yield at an increased processing speed over manual rollers. And because automatic rollers don’t come into contact with human hands, they present a lower chance of contamination, worker injury, and other safety hazards.
On the other hand, while automatic rollers can process products faster, manual rollers allow peeled gizzards to be reworked without further damage, resulting in a higher-quality final product. Manual rollers aren’t as prone to over-processing of products, and are also generally easier for employees to reach than automatics, consequently making them easier to clean and maintain.
TIGHTNESS
The bolts in a roller block assembly may come loose over time, resulting in reduced efficiency. This can generally be fixed by tightening the two bolts at end of peeler head and pushing the blocks together against the rollers.
BLOCKS AND BUSHINGS
To spin effectively, rollers need end blocks to hold them in place and brass bushings that act as lubricating sleeves to keep them from vibrating or coming loose. The state of the blocks and bushings have a big impact on the overall effectiveness of the roller itself: even a roller in excellent condition will not perform properly and even be damaged if it is attached to old and worn-down blocks or bushings.
Bushings should be replaced every two weeks, while blocks should be replaced every four months. In addition, you should also replace your bushings every time you replace your rollers. Changing your bushings will lengthen the life of your rollers as they protect from premature wear on the shafts and give lubrication for even performance.
OTHER MACHINERY
The other machinery in your plant can also affect your rollers. For example, in the gizzard area, gizzards will move through the harvester and defatter before peeling; if either machine is damaging the product, the gizzard could come out already in pieces or improperly cut. Peeling gizzard with these sorts of defects can damage them further, and as a result your plant will suffer a lower yield.
In addition to the direct effects of a defective machine, rollers can also be indirectly affected by the location of other machines in the floor layout. The smaller the floorspace that the maintenance team has to work with and the more hard-to-reach areas present, the harder it will be to clean the rollers effectively, meaning that they’ll be worn down much more quickly.
SAFETY
As always, safety should be priority number one at any food production plant. While there is a misconception that rollers are dangerous, the truth is that they’re perfectly safe so long as guidelines are in place and employees have had proper training. However, having these safety protocols in place will also lead to larger product yields and bigger profits.
Before you peel a gizzard, be sure to inspect it thoroughly first for any damage or faults. Before peeling, split the gizzard with a knife or with pneumatic scissors, which you might consider permanently mounting horizontally, with the blade facing upward. This may not be necessary if you have a gizzard harvesting machine.
Never wear gloves while operating a roller, as the material can get pulled into the peelers, potentially causing injury. Likewise, avoid long sleeves, loose shirts, or smocks, and keep those fingernails trimmed and short. Apply pressure to the gizzard with the horizontal flat part of your palm and the bottom of your fingers only. Take care not to press the tips of your fingers inwards or towards the rollers.
Don’t create a roller cleaning plan without taking the overall plant layout into account. Keeping certain pieces of equipment too close together can create areas that are hard to see or out of reach, making them harder to clean effectively. Inspect each machine carefully for these types of areas and instruct all employees on how to properly get to them.
CLEANING AND MAINTENANCE
Like every piece of equipment, the rollers that produce the best yields & highest returns are the ones that are conserved through cleaning & maintenance.
THE BENEFITS OF CLEAN, MAINTAINED ROLLERS
Rollers, like any machine, last longer the better they are maintained, and the importance of keeping rollers clean cannot be overstated.
Unclean rollers that are left to sit out will gradually collect rust, dirt, and animal fragments. If these contaminants are left to build up for too long, eventually a breakdown is inevitable. By adhering to a strict cleaning and maintenance schedule, small problems won’t have a chance to snowball into big ones, and you’ll be able to give your rollers a much longer operational lifespan.
In addition to working longer, cleaned and maintained rollers will also work better. The same contaminants and buildup that can gradually kill a roller can also cause it to dull and perform poorly. The result is that clean and well-maintained rollers can not only cost you less in terms of repair, but can make your plant more money both in product quality and in overall product yield.
KEEPING ROLLERS CLEAN
Rollers should be cleaned every night during the sanitation shift. This is accomplished by thoroughly spraying each set of rollers with highlypressurized water. Having each set of rollers running while being sprayed down ensures that nothing is missed and that every part of the roller gets an even treatment.
Always keep an eye out on the water supply used for cleaning and lubrication. Under each machine, there is a 3/8” water supply feeding a water bar that provides a steady water supply to each set of rollers.
This ensures that water sprays on the bottom side of the rollers, keeping gizzards from floating on the water on top of rollers. If this bar is broken or missing, it will need to be replaced as soon as possible.
ROLLER MAINTENANCE
In addition to keeping rollers clean, it’s also vital to keep them well maintained and working properly. Have your maintenance team thoroughly trained on all of the ins and outs of each roller set in your plant, paying particular attention to probable situations that can arise and how they can be fixed.
As time passes, consumer demand continues to rise, making machine breakdowns and the associated opportunity costs that much more painful. This has led many plants to start organizing plant processes with predictive maintenance in mind.
Predictive maintenance hinges on keeping downtime and maintenance costs as low as possible by identifying and eliminating any potential problems as early as possible, before they can fester and cause long-term damage. Consider looking into vibration analysis and thermal imaging software, which can interpret problem signs invisible to the naked eye, giving managers more time to develop an effective solution.
One crucial but often overlooked factor in effectively maintaining a roller is the quality of bushings and blocks being used. Check out the section “Roller Replacement” for more information.
REFURBISHING YOUR ROLLERS
While only certain types of rollers (neck skinning) can be restored instead of outright replaced, refurbishing your plant’s rollers remains a viable option to getting the longest possible effective lifespan out of them.
The Benefits of Refurbishing Rollers
As with proper cleaning and maintenance, the core concept behind refurbishing your plant’s neck skinning rollers is to keep them working better for longer. Namely, the benefits of refurbishing rollers include, but are not limited to:
-
Longer lifespan
-
Greater product yield
-
Reduced chance of breakage and downtime
-
Reduced chance of machinery cross-contamination
-
Reduced cost compared to replacement
Factors to Consider When Refurbishing
If you’re thinking about refurbishing your plant’s rollers instead of replacing them outright, here are some factors to take into account before making a decision:
TYPE OF ROLLER
Because of the way they are designed, as a general rule, only Neck Skinning Rollers can be refurbished.
TIME FRAME
Normal wear time for a roller is 6-8 weeks. Refurbishing a pristine roller before any wear and tear has occurred is a waste of money; on the other hand, wait too long and you might as well replace it altogether.
TEETH CONDITION
The general rule for refurbishing a roller instead of replacing pertains to the condition of its teeth. If the teeth are still sharp and effective but the shaft is worn down, refurbishing is in order. If the teeth are dull or broken, it’s time to replace.
CURRENT ROLLER EFFECTIVENESS
Ultimately, the debate over whether to refurbish or replace is decided by the needs of the plant. Not all rollers are created equal; if you’re already using the best rollers available, by all means refurbish them and get your money’s worth. However, if higher quality or more cost-effective rollers become available, consider trading up.
ROLLER REPLACEMENT
Even the best roller breaks down eventually. By knowing the proper timeframe to expect a breakdown and taking the correct precautionary steps, you’ll be able to get the most out of today’s rollers before you have to change them.
WHEN TO REPLACE
The typical lifespan for a given roller is 6-8 weeks. Any roller that can’t be refurbished should be replaced somewhere in this time, and no roller should stay on the line longer than two months.
Teeth are the key factor in replacement. Regardless of how long it’s been in use, any roller that has teeth with more pits than can be repaired should be replaced immediately. If the pits are more than one-fourth inch of the teeth depth and more than one-fourth of the roller’s overall teeth surface, its entire effectiveness has been compromised, and it’s time to buy a new set.
Don’t forget that, in addition to the rollers themselves, the blocks and bushings that rollers need to operate effectively will also need to be changed out regularly. In addition to adhering to a strict cleaning and maintenance schedule, the best poultry production plants have systems in place to ensure bushings are replaced every two weeks and blocks every four months.
SIGNS IT’S TIME TO REPLACE
While 6-8 weeks is the general rule for replacing a current roller with a new one, there are a few other factors that can send a roller to an early grave. On your next maintenance check, be on the lookout for:
BROKEN OR DEPLETED FUNCTIONALITY
Like any other piece of machinery, a roller can be subject to vibration, shock, and high temperature during day-to-day operations of the plant. Sometimes, these factors can age rollers prematurely and eventually cause them to lose functionality, at which point it’s time to replace.
SKIN AND FAT BUILDUPS
Buildups of skin and fat are another classic warning sign of a faulty piece of machinery. During scheduled maintenance checks, if you or an employee finds areas with excessive buildups, it’s usually a sign that significant wear-down has occurred, and that it’s time to replace.
WORN TEETH
Dull teeth are the biggest killer of poultry rollers in the industry. No matter how well maintained, if the roller can’t peel and skin poultry effectively, it has no place in your plant.
With over 40 years of experience in the industry, DeLong’s is one of the leading authorities on poultry processing rollers in the United States. Our rollers are some of the best in the industry, providing you with safer processes, higher yield, and a better bottom line. No matter how well-maintained, rollers at your plant have to be replaced after about eight weeks. DeLong’s is always on call to help, and we offer on-site consultation and training to make sure your rollers and poultry processing procedures are as efficient and productive as possible. Are you looking for ways to increase yield at your plant? Schedule a Consultation with a Delong’s expert today.
SOURCES
- Poultry Processing Industry eTool
- Poultry Products Processing: An Industry Guide
- Scalding and Plucking for Optimum Carcass Quality and Yield
- Responsible Disposal of Hatchery Waste
- Poultry Processing: Questions & Answers
- How to Find Efficient Poultry Processing Equipment
- How to Know When to Replace your Poultry Processing Parts
- DeLong’s Products