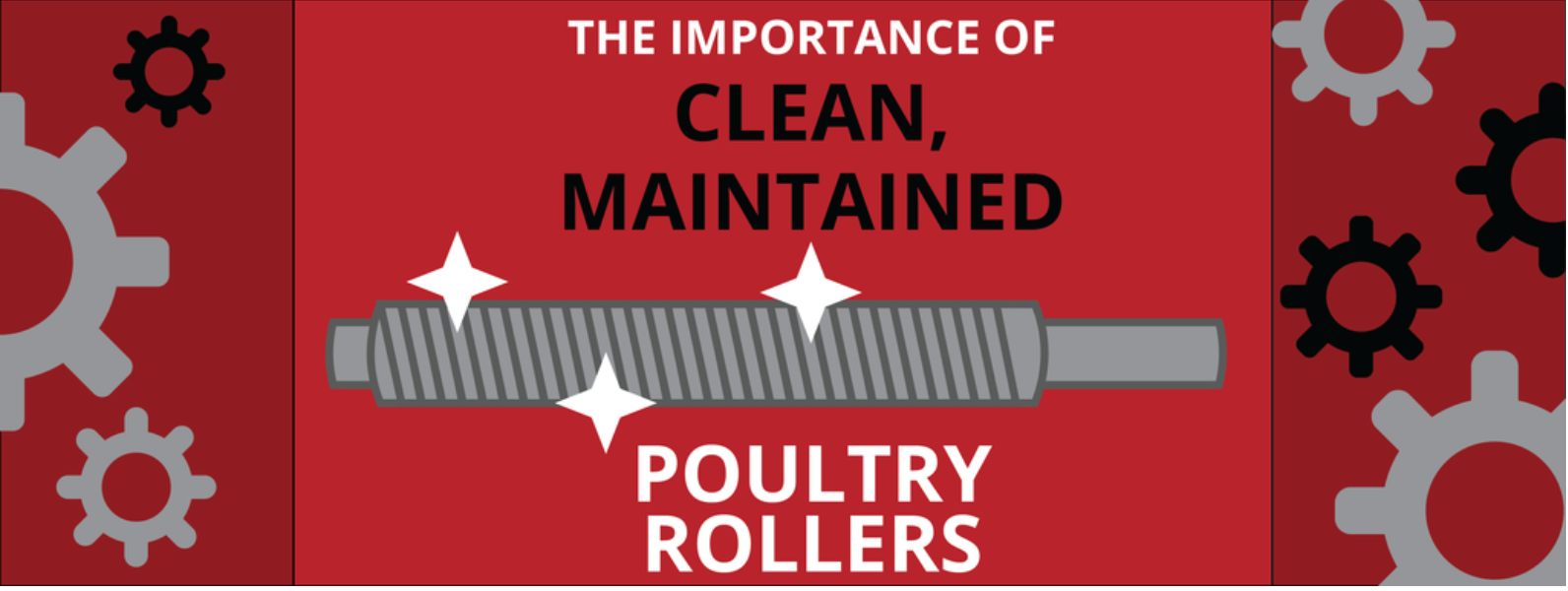
03 Oct The importance of clean, maintained poultry rollers
Rollers, like any machine, last longer the better they are maintained, and the importance of keeping rollers clean cannot be overstated. Like every other piece of equipment, the rollers that produce the best yields and highest returns are the ones that are conserved through cleaning and maintenance.
Unclean rollers that are left to sit out will gradually collect rust, dirt, and animal fragments. If these contaminants are left to build up for too long, eventually a breakdown is inevitable. By adhering to a strict cleaning and maintenance schedule, small problems won’t have a chance to snowball into big ones, and you’ll be able to give your rollers a much longer operational lifespan.
In addition to working longer, cleaned and maintained rollers will also work better. The same contaminants and buildup that can gradually kill a roller can also cause it to dull and perform poorly.
The result is that clean and well-maintained rollers can not only cost you less in terms of repair, but can make your plant more money both in product quality and in overall product yield.
Keeping Rollers Clean
Rollers should be cleaned every night during the sanitation shift. This is accomplished by thoroughly spraying each set of rollers with highly-pressurized water. Having each set of rollers running while being sprayed down ensures that nothing is missed and that every part of the roller gets an even treatment.
Always keep an eye out on the water supply used for cleaning and lubrication. Under each machine, there is a ⅜” water supply feeding a water bar that provides a steady water supply to each set of rollers.
This ensures that water sprays on the bottom side of the rollers, keeping gizzards from floating on the water on top of rollers. If this bar is broken or missing, it will need to be replaced as soon as possible.
Don’t create a roller cleaning plan without taking the overall plant layout into account. Keeping certain pieces of equipment too close together can create areas that are hard to see or out of reach, making them harder to clean effectively. Inspect each machine carefully for these types of areas and instruct all employees on how to properly get to them.
Roller Maintenance
In addition to keeping rollers clean, it’s also vital to keep them well-maintained and working properly. Have your maintenance team thoroughly trained on all of the ins and outs of each roller set in your plant, paying particular attention to probable situations that can arise and how they can be fixed.
As time passes, consumer demand continues to rise, making machine breakdowns and the associated opportunity costs that much more painful. This has led many plants to start organizing plant processes with predictive maintenance in mind.
Predictive Maintenance
Predictive maintenance hinges on keeping downtime and maintenance costs as low as possible by identifying and eliminating any potential problems as early as possible, before they can fester and cause long-term damage.
Consider looking into vibration analysis and thermal imaging software, which can interpret problem signs invisible to the naked eye, giving managers more time to develop an effective solution.
One crucial but often overlooked factor in effectively maintaining a roller is the quality of bushings and blocks being used. Check out the section “Roller Replacement” for more information.
Looking for more great tips and strategies you can use to push your poultry rollers further? Check out our free informative guide, The Lifecycle of a Poultry Peeling Roller, and push your poultry production plant further today!