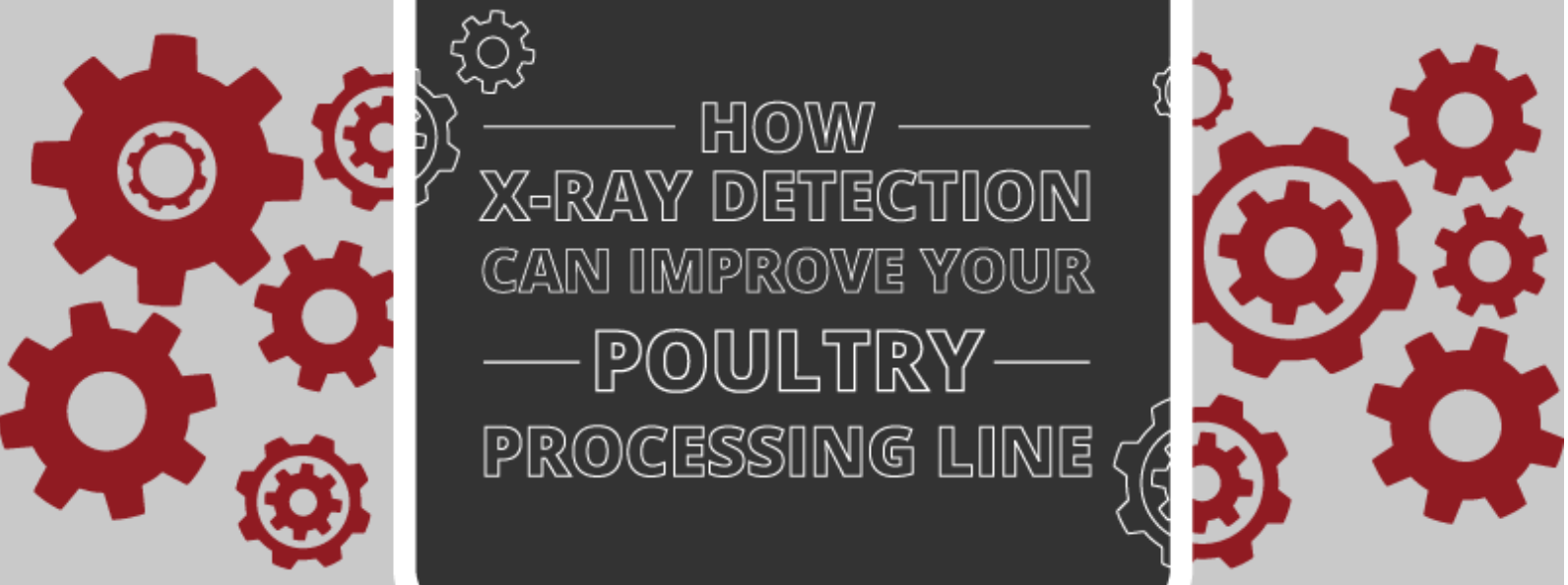
16 May How X-Ray Detection Can Improve Your Poultry Processing Line
Poultry production is a growing and ever-changing industry, but some things remain constant: deadlines have to be met, and the product has to come out contamination-free. As demand continues to increase, managers of poultry production facilities constantly have to find faster and better processes in order to keep up.
Unfortunately, it’s not as simple as just speeding up the production line. The faster things are running, the more likely an accident becomes, and downtime from broken equipment can cripple or even sink a company. However, X-ray technology can help prevent damaged machinery, product contamination, and product defects. This blog is a summery of Gainco’s guide to Choosing The Best Poultry X-Ray Detection Process. We strongly recommend that you read their report.
Limitations Of Modern Poultry Processing
In recent times, a shortage of knowledgeable employees has made staffing much more difficult for poultry production plants. In response, many facility managers have begun to incorporate more and more automated deboning processes into their plants to supplement manual labor.
However, automated deboners are not perfect. Metal detection is still one of the most commonly-used processes, but obviously this only detects metal fragments in the meat, not other materials such as bones.
For the most part, visual inspection is still necessary for detecting bones, but this presents two key problems. The first is that visual inspection is an imperfect process, and bones that are deeply embedded in the meat can go unnoticed.
The second problem is that, in an industry with ever-increasing demand but a stagnant pool of qualified employees, automated production lines have to run faster and faster while each employee’s ability to visually identify bone fragments in the meat stays constant.
This has resulted in an unfortunate trend: more automation leads to increased amounts of bones left in products. However, breakthroughs in X-ray technology present a number of potential solutions for poultry plants to create safer, higher-quality products at a lower cost.
So, why use X-ray technology?
Contamination Prevention
X-ray’s biggest draw is its ability, in conjunction with other automated processes, to detect and remove contaminants quickly and efficiently. Where metal detectors are limited in scope and the human eye can miss hidden bones, X-ray combines the best of both worlds.
X-rays allow workers to see beyond the surface and get a better picture of what lies beneath, helping prevent recalls by ensuring that only contaminant-free final product reaches the public.
Prevent Damage to Machinery
Beyond potential recalls and the negative press that comes with them, X-ray technology also helps keep the plant up and running.
Pieces of bone can rip into conveyors, get caught in machinery, and cause all manner of problems in a poultry’ plant’s machinery. Because it can detect potential hazards early in the production process, X-ray can help workers stop the problem before it happens.
Prevent Defects
Finally, X-ray technology can help detect defects in product shapes and packaging that might go unnoticed to the naked eye. This helps managers identify any less-than-optimal pieces before they get too far into the production process so that only the best pieces get shipped.
Not only can X-rays provide a safer product, they can produce a better product to boot.
Learn more about X-Ray Detection in poultry processing in Gainco’s guide: Choosing The Best Poultry X-Ray Detection Process.
Interested in learning more about ways you can increase your poultry plant’s safety, efficiency, and output? Download our free Ebook, Why and How to Cross-Train in Maintenance and push your plant to the next level.