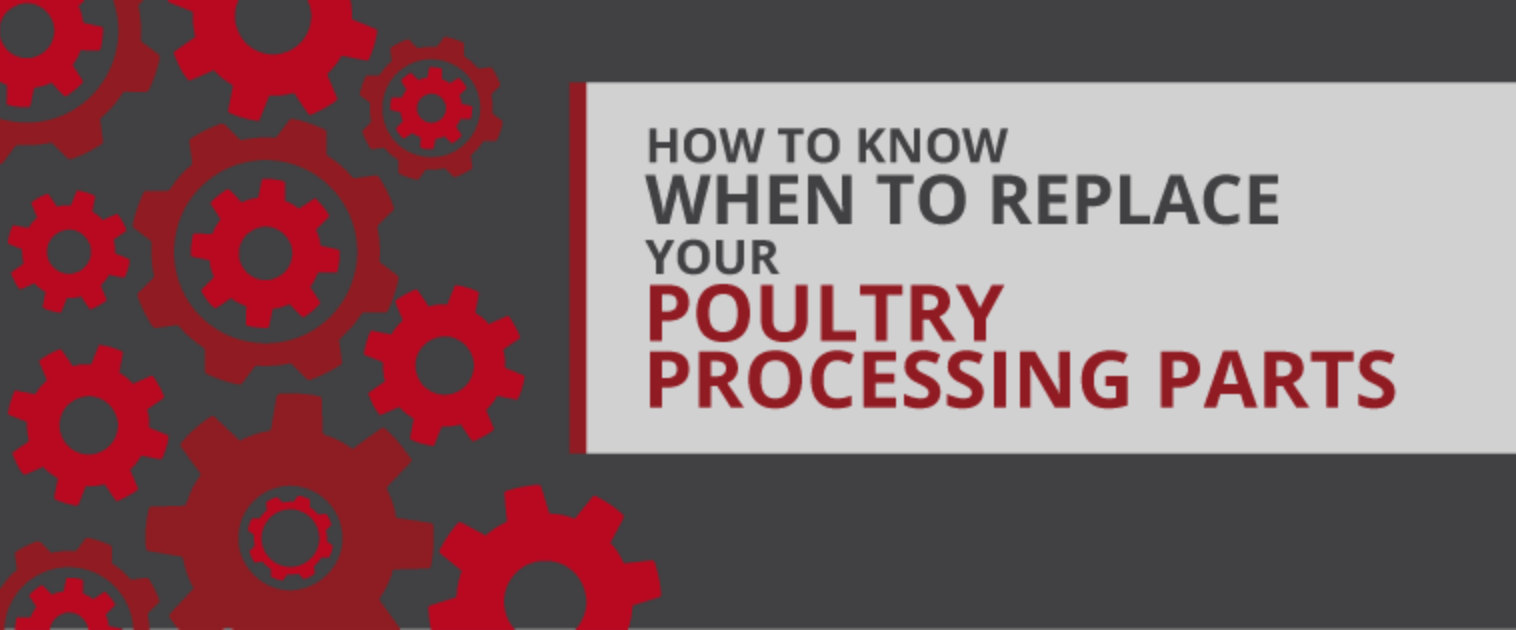
07 Apr How to know when to replace your poultry processing parts
Machinery breakdowns are inevitable. In order to reduce your chances of a breakdown, you must monitor and replace parts before they lead to a larger problem. There are a number of ways to go about this, and this blog offers a guide to the monitoring, detection, and replacement of your processing parts.
Reasons For Replacement
There are many factors that can lead to the breakdown/deterioration of your equipment parts. Here are 3 primary reasons that constitute the replacement of your processing equipment:
-
Depleted Function/It’s Broken
- Vibration, shock, and high temperatures can lead to machinery breakdowns. It’s important to assess your equipment to make sure that it’s running properly, and take corrective measures if you’re experiencing an issue.
- Check lubrication- when running a maintenance check, look for signs of excess oil or grease build ups. Analyzing the particle content of the used oil will allow you to see if there are contaminants resulting from worn-down or malfunctioning equipment (Manufacturing Transformation).
-
Deterioration Due To Aging
- Outdated equipment will naturally deteriorate and lose its functionality. It’s important to detect signs of aging equipment and replace as needed.
-
Equipment Is Obsolete
- If you’re operating with outdated equipment, you might be losing efficiency. Replacing old equipment with Updated or improved parts might allow for a more effective process and improve overall performance.
Predictive Maintenance Methods
Now that you know what factors affect the lifespan of your machinery parts, it’s essential to check these areas regularly to prevent breakdowns. Our recommended methodology is Predictive maintenance. Predictive maintenance involves taking constant measures to assess your plant’s machinery, and identifying problems before they arise. This will allow for a more efficient operation, as you reduce downtime with fewer breakdowns. According to Lean Manufacturing Tools, here’s two predictive maintenance methods that will help you manage your equipment:
-
Vibration Analysis
- When machinery parts are worn, they will give off different vibration patterns. Using built in monitors, or handheld vibration analyzers, you can detect these patterns as they arise, and take proper action.
-
Thermal imaging
- Malfunctioning circuitry and worn equipment tend to give off extra heat. With the use of thermal imaging, you will be able to detect these “hot spots,” and determine which parts need attention.
Economic Evaluation
Once you’ve identified which parts need replacement, you must determine what fits into your budget. If the piece is essential, replace it immediately. If the piece is obsolete/non-essential to your operation, you should assess the needed parts, and prioritize replacement based on relative importance.
The best way to assess the your replacement needs is to create a detailed spreadsheet that hilights your budget and lists individual parts, sorted by operational importance. When determining the value of each item, it’s essential to consider the productive and financial outcome of replacement. Once you’ve created a spreadsheet and you’re ready to make purchases, you simply move through the list, selecting items to replace until you’ve fulfilled your budget. This will ensure that you reduce spending on unnecessary items, and focus on what’s essential to your process (Cal Poly).