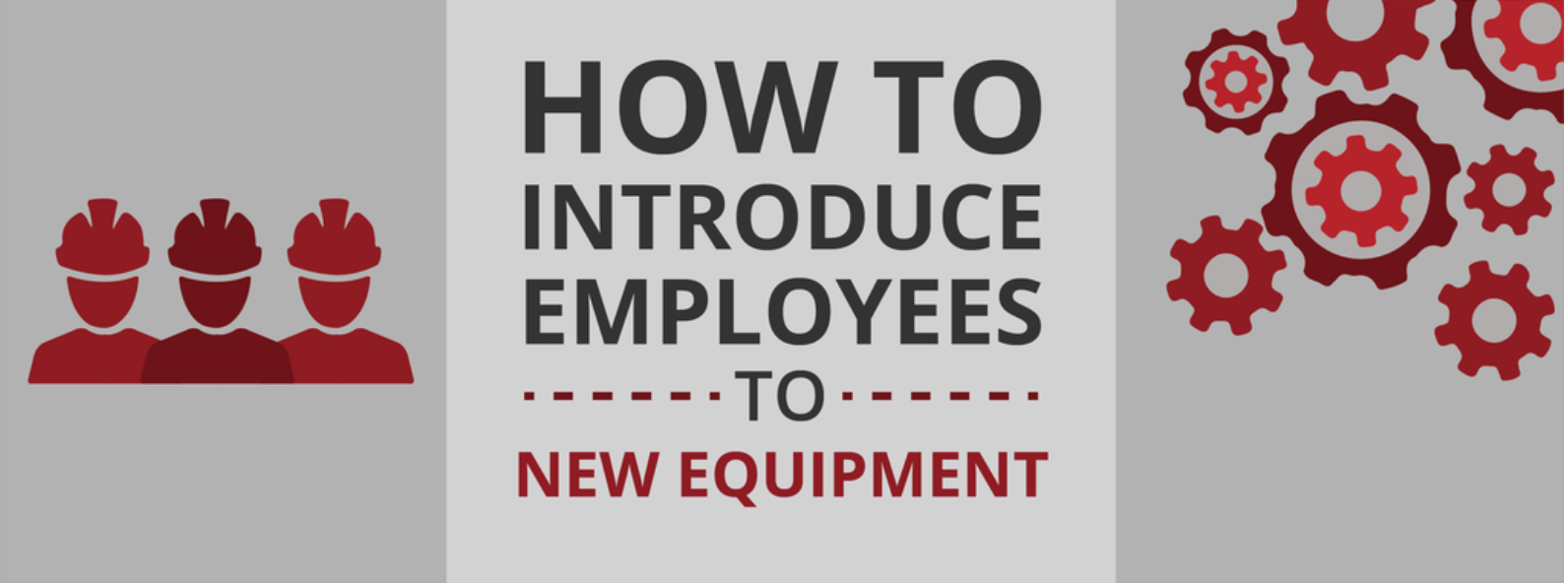
10 Aug How To Introduce Employees to New Equipment
Introducing employees to new equipment isn’t always easy. While upgrades will always be necessary to stay ahead of the competition, some employees won’t adapt as quickly as others. Some may resist the change completely.
Properly introducing and training your plant’s employees on new equipment is an essential part of operations. After all, what good is new equipment if none of your employees can use it effectively?
Here are some good strategies you can implement to ease the transition at your poultry production plant:
Know Your Needs
Before you upgrade your plant’s equipment, it’s imperative that you know exactly why you’re making the change in the first place. Afterall, when it comes to workplace safety and productivity, enacting change just for the sake of change is one of the worst mistakes you can make.
As a manager, you should be able to explain in no uncertain terms precisely why you’re introducing the new equipment. If you can’t give an adequate explanation why the existing equipment is suboptimal and which shortcomings the new equipment seeks to eliminate, take a step back to reconsider if the benefits of an upgrade are worth the cost.
Make a Plan, Follow It
So, you’ve discovered a problem and identified a solution in the form of a new piece of equipment. However, you still won’t be able to fully sell your employees on the change if you can’t produce an actionable plan that details exactly how the new equipment will be implemented.
The more detailed the plan, the better. A lot of the resistance people feel when introduced to new things is simply fear of the unknown. By going into fine detail about every part of the new equipment implementation plan, you’ll put your employees’ minds at ease and help make them enthusiastic about the transition.
Minimizing Resistance
Change doesn’t always come easy. Just because a new, more-effective system has been implemented doesn’t mean people will immediately appreciate it. People can be resistant to change, especially when they don’t understand the reason for that change.
When you outline the new plan to your employees, make sure to emphasize that the steps being taken are to create a safer and more-productive workplace. Remind your employees that, while it’s frustrating to adapt to new processes and unfamiliar equipment, this is a change meant to make their lives easier in the long-run.
Most importantly, be patient. Different people adapt to change at different speeds, and getting angry at employees that are struggling to keep up will put more pressure on them and make the situation worse. Instead, take the time to understand where they’re having problems and help them reach a solution. New policies take time to gain acceptance, so give employees a little room to adjust.
For more information about how to equip your plant’s team for success in the changing world of poultry production, download our free informative Ebook, Why and How to Cross-Train in Maintenance today!