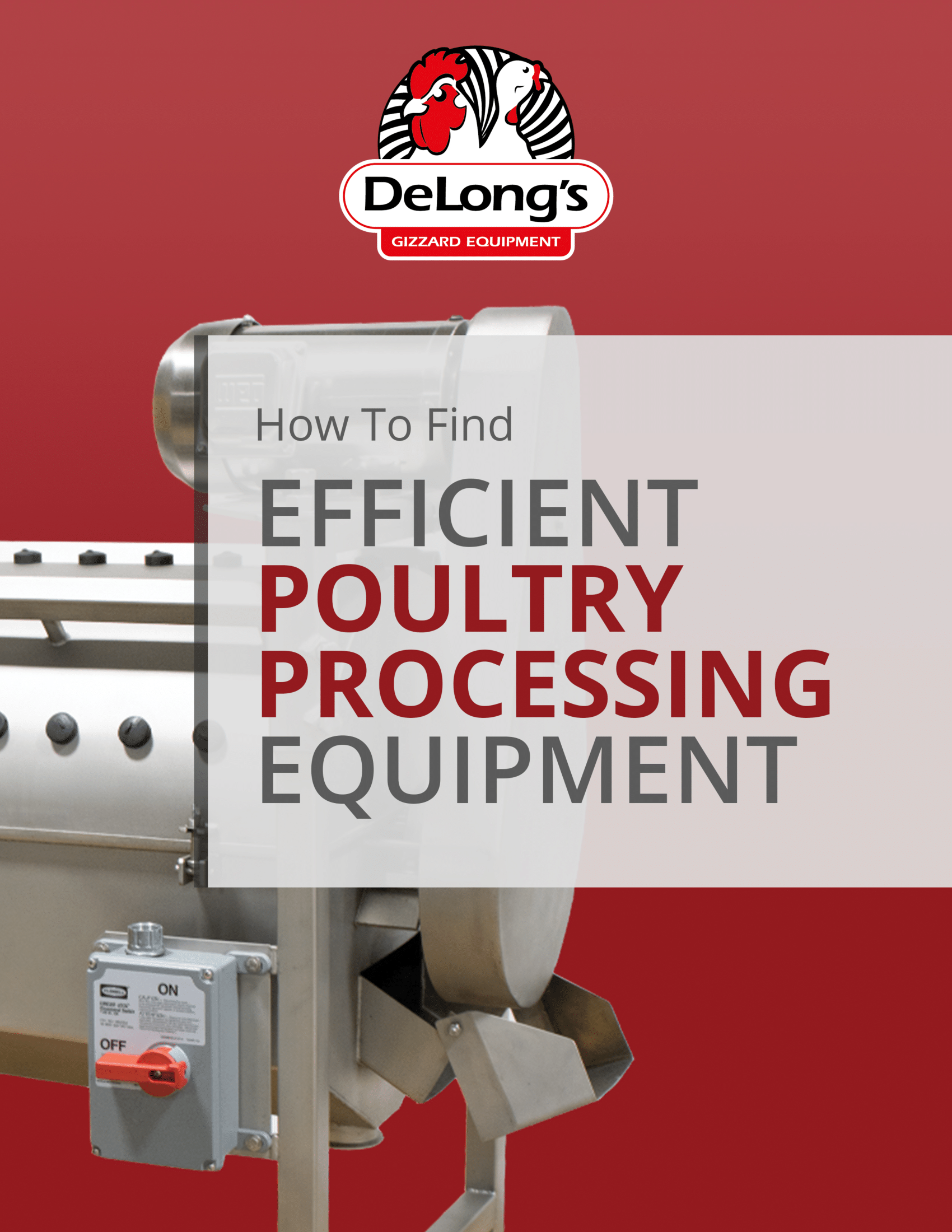
21 Dec How to Find Efficient Poultry Processing Equipment
With increasing feed costs and staggering meat costs, it’s more important than ever to invest in more cost efficient machinery. This guide will give you some practical ways to make sure your plant is stocked with equipment that will help you increase yield, minimize downtime, and decrease maintenance costs.
1. Consider a Multi-Purpose Solution
Multi-Purpose machinery offers a range of benefits to poultry processors. This chapter will look into how multi-purpose machinery can:
- Lower factory footprint and increase floor space
- Lower machinery costs
- Reduce human error
- Decrease downtime
Facing machinery clutter?
Having lots of machines clutter your facility means:
- Less space
- More money spent purchasing unique equipment
- Less efficient workflow
- More frequent maintenance
- More spare parts needed
Implementing multi-purpose machinery is a great way to combat all these problems.
Lower factory footprint and increase floor space
Floor space is integral to a safe, clean, and efficient plant. Increased floor space allows for:
- Reduced chance for worker injury – workers are able to keep a safe distance from dangerous machinery more easily
- Increased mobility – workers are able to move freely throughout the plant
- Increased cleanability – sanitation crews can access all parts of the plant and machinery, giving them the ability to clean more quickly and efficiently
- Make repairs and replacements easier – with more space around machinery, it’s easier for personnel to work on machinery and replace parts without having to move and/or disassemble equipment.
Lower machinery costs
Both manual and automated processing lines have weaknesses that increase costs and lower yield. Automated lines have more downtime, while manual lines are more hazardous and require higher worker compensation.
Multipurpose machinery allows you to automate processing lines while reducing downtime caused by mechanical errors. Multipurpose machinery reduces the number of machines that can malfunction, and reduces the amount of replacement parts needed. For these reasons, multipurpose machinery can be a more cost effective option.
Less human interaction required
Human interaction inevitably leads to human error, and human error can result in harm to workers, products, and overall productivity.
The CDC estimates that 128,000 people are hospitalized and 3,000 die every year from foodborne illnesses of all causes. A study from 2015 found that meat recalls cost a food processing company an average of $109 million in the first 5 days after the announcement.
Automating your processes can create a safer and cleaner environment and reduce the chances of contaminated product.
Automation can also:
- Cut down on labor costs
- Increase processing speeds
- Achieve more predictable yield
- Reduce water and energy expenses
Decrease downtime during equipment failure
Having machines that can do each other’s job, and having backup machines on hand can reduce downtime considerably during equipment failure.
2. Do a Spare Parts Analysis
The number of parts a machine has, their price, the time it takes to replace a part, and the importance of those parts in a machine’s productivity should always be considered when purchasing new equipment. This chapter will walk you through how to assess a machine’s parts and how to use that information to inform your buying decision.
Assessing Parts
While considering the purchase of a new machine, it’s important to understand how many parts that machine has. Is this new machine replacing existing machinery? If so, consider if this new machine has more or less parts than the machine it will replace.
The fewer parts a machine contains, the fewer parts you need to have on hand in case of mechanical failure, and the more money you can save.
Think about how the hardware you are considering compares to other on-hand equipment.
- Ensure it uses the same measurement system. Does the machine you’re considering use metric or imperial system for measurements? If possible, you want all of your machinery to use the same measurement to reduce the amount of tools and spare parts needed.
- Does it use similar nuts, bolts and other fasteners to your current machines? Machinery with the same pieces will allow you to cut costs on spare parts.
Assessing Risk
Perform a Critical spare parts analysis to determine a risk based strategy that will allow you to take into account the risk of a part breaking, the cost of the machine, and the cost of downtime.
In order to properly manage risk, you must consider:
- What equipment failure risks are there?
- What are the results of an equipment failure? (injury to workers and other equipment, cost of repair, downtime to make repairs)
- What is the probability that equipment failure will happen? (Manufacturer warnings, statistics, etc.)
- How can you prepare for or eliminate the risk of equipment failure? (Having parts on hand, buying insurance, etc.)
- Are there any additional risks when equipment takes longer to repair than expected?
Use the following charts to determines if a part needs to be kept in stock:
Probability Score Matrix
Decision Matrix
Bringing it all together
The objective is to have equipment that is:
- As cheap as possible to buy
- Features cheap replacement parts
- Has the fewest spare parts
- Has a high likelihood of functioning for a long time without requiring maintenance
- Doesn’t take long to repair
Avoid equipment that:
- Is unnecessarily expensive to buy
- Has lots of parts
- Has expensive parts
- Has a high likelihood of malfunctioning
- Takes a long time to repair
You want to make sure you have precisely the right kind and amount of parts you need to properly handle equipment malfunctions in a way that reduces downtime as much as possible, and ensures the highest yield and safest environment.
3. Consider a Simpler Machine
The most high-tech machinery isn’t always the best option. Complex machinery is:
- More difficult for personnel to operate properly (requires more training)
- Is more time-consuming to repair
- Is more difficult to clean
This section will explain how simple machinery can help you save cost in a number of areas and will give some key traits that cost effective machinery should have.
Ease of Use
In some cases complex machinery is unavoidable. But, the more complex a machine is, the more training staff will have to have in order to properly use it.
The more training that staff have to have in order to properly use a machine, the more money that machine will cost you in hours of training. Also, if a machine is new, training may be difficult to find and expensive. Higher turnover rates can also drive up the frequency of required training.
Ease of Repair
How easy is it to repair a machine? Do you have to disassemble the whole thing just to perform a simple scheduled maintenance? Equipment should be easy to quickly disassemble and reassemble in order to minimize downtime.
While demoing equipment, it’s important to ask what regular maintenance entails, and how long regular maintenance should take.
Consider the downtime necessary for repairs when looking at the overall cost of competing machines. A cheaper option that takes longer to repair or maintain may have a greater negative impact on your bottom line than a more expensive option that can be quickly repaired.
Ease of Sanitation
Ensure the machine isn’t too complicated for maintenance crews to effectively sanitize. Here are a few guidelines to keep in mind:
- Validated cleaning and sanitation protocols – Make sure machinery has validated protocols that your staff won’t have any problem following.
- Water and cleaning resistant – Sanitation in a processing plant usually involves everything being sprayed down. Will the new machine handle this without failure? Does it rely heavily on electronics like touch screens that may be damaged by sanitation?
- Stainless steel surfaces – Any surface that is in contact with product should be stainless steel.
- Easily accessible – Make sure that all the surfaces that are in contact with food are easily accessible and cleanable (unless they have a CIP).
- Joints and fittings – Any joints and fittings should be designed for easy sanitation.
Does it come with a Clean-in-place system (CIP)? Some machines are built with self-cleaning high-pressure pumps that shoot water and cleaning solutions through equipment for easy cleaning.
4. Consider All the Available Options
When looking for the best equipment, it’s important to check online directories for all available options. There are a lot of industrial manufacturing directories out there, some better than others. Here are a few good ones to start with:
Thomasnet.com – Thomasnet is an incredibly in-depth and user-friendly free directory for industrial manufacturers. The website includes detailed company profiles and is easily searchable, featuring a total of 660,000 OEMs, industrial custom manufacturers, distributors, and service companies.
Search by product or service category, location, UNSPSC commodity code, ownership, quality certification, or company type.
Thomasnet claims to have consolidated 100 million items from 200 thousand catalogues into a single, searchable database.
World of Manufacturers – Not quite as comprehensive as Thomasnet, but free and useful none-the-less, worldofmanufacturers.com allows you to search thousands of companies for the perfect product to meet your manufacturing needs.
More directories worth checking:
- manufacturerusa.com/
- manufacturersupplier.com
- industrialquicksearch.com/
- manufacturing.net/
SOURCES
- http://www.meatingplace.com/Industry/TechnicalArticles/ Details/53147
- https://www.lce.com/The-Role-of-Critical-Spares-Analysis-inValidating-Spare-Parts-Recommendations-1364.html
- https://www.technologyreview.com/s/537646/robots-start-tograsp-food-processing/
- http://www.agmanager.info/costs-meat-and-poultry-recallsfood-firms
- http://reliabilityweb.com/articles/entry/spare_parts_ inventory_an_exercise_in_risk_management
- http://www.meatingplace.com/Industry/TechnicalArticles/ Details/60404
- http://www.foodsafetymagazine.com/magazine-archive1/ augustseptember-2005/top-7-processing-and-foodserviceequipment-standards/