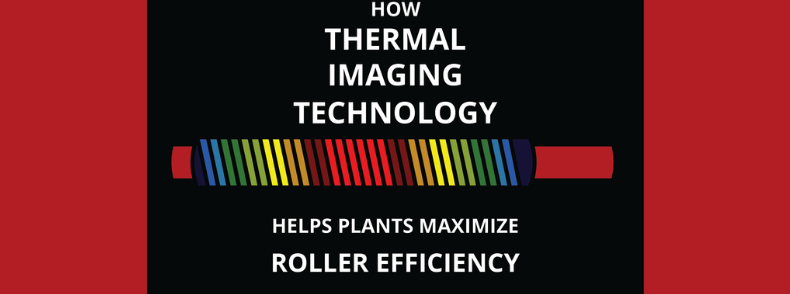
14 Nov How Thermal Imaging Technology Helps Plants Maximize Roller Efficiency
Poultry plant managers are always on the lookout for ways to avert costly failures and get higher yields and better efficiency out of their existing equipment, namely their plant’s poultry rollers. Every roller will need to be replaced eventually, but proper cleaning and maintenance or refurbishment are two well-known practices within the industry to give rollers longer, fuller lifespans.
However, as production methodology continues to adapt and improve into the 21st century, many plant managers and engineers are turning to new and emerging technologies to increase plant efficiency. In our previous two-part blog series, we explored one such technology gaining traction in the industry: vibration analysis technology, and the many benefits it brings.
Thermal imaging is another emerging technological innovation that many managers are utilizing in their plants. In this blog, we’ll take a look at thermal imaging technology, how it works, and how plants can use it to maximize poultry roller efficiency in their plants.
What Is Thermal Imaging?
Thermal imaging is a classification of non-invasive imaging that uses infrared rays to detect radiation patterns and display them as pictures known as thermograms. Any object with a temperature higher than absolute zero (effectively any object on earth) emits infrared light that is invisible to the human eye; thermal imaging simply allows us to “see” this light and interpret it.
Thermal imaging cameras work by measuring the amount of energy they “see” and converting it into a temperature measurement, which displayed as a color that humans can see. Because the radiation emitted by any object increases with its temperature, thermal imaging allows the viewer to see variations in temperature across any object or objects in the field of view – with each individual color representing a specific temperature.
Put simply, thermal imaging allows users to “see” temperature. But unlike traditional non-contact infrared thermometers, which provide a single average heat measurement of the area it covers, thermal imaging takes tens of thousands of measurements a second so viewers can see precise measurements of each individual object in the field of view.
Thermal imaging technology has been used for military and surveillance purposes for decades, but as the potential applications are better explored, it is seeing more and more integration into other fields – namely poultry production.
How It Works
Thermal imaging follows five basic steps:
- An infrared camera uses a special lens capture and focus all of the heat signatures emitted by all the objects in its field of view.
- The focused light is scanned by a phased array of infrared-detecting elements and within one-thirtieth of a second obtains temperature information from several thousand points in the field of view of the detector array in order to create a detailed temperature pattern called a thermogram.
- The thermogram is translated into electric impulses and sent to a signal processing unit.
- The signal processing unit uses a dedicated chip to translate the information received from the thermogram into data that can be interpreted by the display.
- The data is received by the display and appears as a combination of all the impulses from all of the elements using colors that are visible to the human eye, with each color representing a different temperature.
Taken as a whole, the viewer can then easily see exactly how much heat radiation each object or element captured in the thermogram is giving off.
Thermal imaging devices come in two principle types:
- Un-cooled, the most common type, in which the infrared detector elements are contained in a unit that operates at room temperature.
- Cryogenically cooled, which store their elements in a container that cools them to below freezing temperatures. While cryogenically cooled devices are both more expensive and more fragile than their un-cooled counterparts, they offer far superior resolution and sensitivity, with the ability to detect temperature differences as small as 0.1° C from distances of over 300 meters.
Uses In Poultry Processing
As the technology continues to see increased adoption in the poultry production industry, it has seen use in a growing number of applications, including but not limited to:
- Measuring factory floor temperature
- Analyzing heat loss and gain from poultry houses
- Measuring egg temperatures in incubators and hatcheries
- Managing bird heat stress
- Evaluating radiant heating systems and insulation
- Measuring temperature stratification, air inlet flow patterns, and evaporative cooling system efficiency
For poultry rollers, thermal imaging is a great way for managers and engineers in the plant to monitor the friction created as a roller spins and use this information to gauge if – and where – problems exist.
More importantly, because thermal imaging is non-intrusive, it allows managers under time or budgetary constraints to get an idea of exactly where their rollers are in the lifecycle without having to take them off the production line for a more thorough inspection. For smaller plants, this can be a lifesaver come crunch time because it can give a manager insight into whether the roller can stay on the line or needs to be taken off before catastrophe strikes.
As with vibration analysis, this can also come into play when buying new poultry rollers. Using thermal imaging, a manager can have two rollers developed by separate manufacturers running simultaneously, and measure how each compares to the other and how much heat is created – then use this insight to help determine which roller will perform better in the long-run.
All in all, with a knowledgeable operator in place, thermal imaging provides yet another effective way for poultry plant managers to leverage emerging technology as a means of increasing efficiency and pulling better yields out of their rollers.
For more great tips and strategies that you can use to get higher yields and a longer lifespan out of your plant’s rollers, download our free informative guide, The Lifecycle of a Poultry Roller, and start seeing higher yields today!