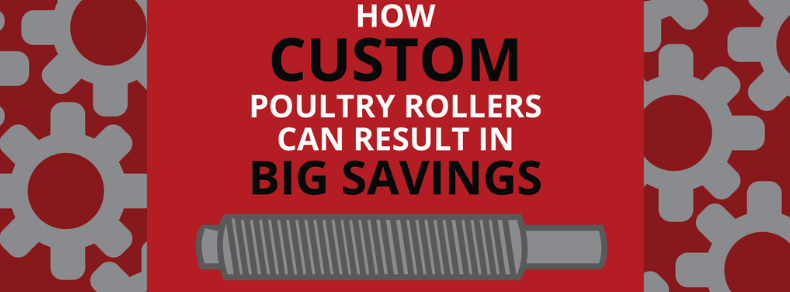
21 Nov How Custom Poultry Rollers Can Result in Big Savings
When it comes to maximizing yields at any poultry plant, few individual components are so essential to success than the poultry peeling machines, more specifically the poultry peeling rollers that perform the actual bird evisceration. Because they hold such a pivotal role, managers are always on the lookout for ways to boost roller efficiency.
While new and developing technologies like vibration analysis and thermal imaging are pushing the industry forward, many managers are also looking inward – getting more out of their older, existing machines. Custom poultry rollers present a cost-cutting and efficiency-boosting measure that can help them do just that.
In this blog, we’ll take a look at customized poultry peeling rollers, the problems they can solve, and the benefits they can bring to poultry plants, both short-term and going into the future.
The Problem With Old Machines
Unfortunately, as we’ve discussed in some of our previous blogs, no roller lasts forever. The maximum recommended lifespan for any given poultry peeling roller is 6-8 weeks; after this point, the roller will become less and less effective until eventually the machine has to be taken off the line so that the old rollers can be taken off and replaced with new ones.
While this usually isn’t a big issue, it can become a major one if your plant operates using older machinery – especially poultry peeling machines that are now out of production. Of course, the problem with older machines isn’t the overall machines themselves but rather the difficulty that comes with trying to find replacements for individual parts.
Just because a machine is older doesn’t mean it can’t get the job done. In fact, with how expensive entire poultry peeling machines can be to replace, it’s common to find plants operating on decades-old equipment. After all, if yields are staying at acceptable levels, why run the risk of taking a working machine off the line to replace it with an expensive new one?
The problem is that most new poultry peeling rollers are made specific to their affiliated machine. If the overall machine is out of production, that means new rollers are too – so even if your existing machine is in working condition and you only really need new rollers, you’ll still be forced to replace the entire machine.
Managers can take steps to maintain their rollers to maximize their effective lifespans, but eventually they’ll be forced to sacrifice an entire functional machine just because of one broken piece.
That’s where custom rollers come in.
Custom Rollers And How Help Plants Save
Customized rollers can help plants tremendously. Unlike traditional machinery manufacturers, custom roller manufacturers can create rollers that are built to fit any size or equipment specification, allowing managers to fix the small problem without having to shell out for an entire replacement machine.
Custom rollers can bring a host of short- and long-term benefits to poultry plants that use them. Some of the biggest advantages to incorporating custom rollers include:
Monetary Savings
On the front end, one of the biggest advantages custom rollers is the expense of machine replacement. Using custom rollers, you no longer have to throw away your older functioning machinery and can instead simply replace the rollers for a fraction of the cost.
Time is also a consideration in this area. Every minute a machine is off the line means a minute that it’s not making money for the plant; since replacing the rollers on a machine is a much quicker process that replacing the entire machine, managers that utilize custom rollers can get their plants back up to optimal production levels in a much quicker time frame.
Higher Yields
One of the benefits of custom rollers is that, while they are made to fit older machines, they are created using the improved processes that have developed over time to make them more effective than ever.
For instance, DeLong’s custom rollers are built with a specific angle on the teeth to make them more aggressive, giving them better peeling action than a traditional factory model. This means that not only can you keep a working machine on the line without having to replace it, but can actually bring it up to the standard of modern machines.
Refurbishment
Custom rollers can not only save you from having to replace the whole machine but can even save you the cost of replacing individual rollers. In addition to creating brand new rollers, many custom roller manufacturers can also refurbish certain types of rollers, bringing them back up to like-new efficiency for even less than the cost of replacement.
While refurbishment is a complicated process and only certain types of rollers can be refurbished, refurbishing where possible can result in big savings.
Gizzard harvester transport rollers, for example, often come with a hefty price tag ranging from $3,000-$4,000 a piece. By sending them in for refurbishment, managers can have their existing rollers’ shafts rewelded and teeth re-sharpened back to like-new quality for a fraction of the cost.
The bottom line: for budget-conscious poultry plant managers looking to get a longer effective lifespan out of their existing machines, custom rollers present incredible potential for savings.
If you’re interested in learning more about what makes for an effective poultry peeling roller, and how you can push your roller towards greater yields and higher efficiency, check out our free informative guide, The Anatomy of a Poultry Peeling Roller, for great tips and strategies you can use to push your rollers further.