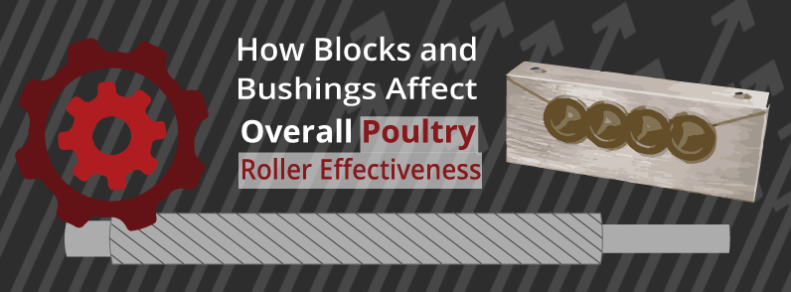
12 Dec How Blocks and Bushings Affect Overall Poultry Roller Effectiveness
There are a host of factors that can be used to ascertain a poultry roller’s quality, such as the condition of the shaft, automatic vs manual action, teeth condition and sharpness, and material construction, among others. However, while all of these factors are important, most are also readily apparent after a thorough regular inspection and maintenancepractices.
On the other hand, two key components are often overlooked: the end blocks and the bushings.
Blocks and bushings are separate from the roller itself, and consequently don’t always get the same attention as the centerpiece. Nevertheless, these elements play a huge role in overall roller effectiveness: even a brand-new high-quality roller won’t be able to perform very well if it’s hampered down by poor blocks or mismatched bushings.
In this blog, we’ll take a look at your rollers’ blocks and bushings, the crucial role they play, and how you can make the most out of the blocks and bushings at your poultry plant.
Roller End Blocks
As the name suggests, the end blocks are solid blocks that each end of the roller shaft is fitted into. At their most basic, blocks hold the rollers in place and allow them to spin effectively, but their overall impact is more nuanced.
Most rollers work in pairs, so most blocks are fitted with two holes each (though four-hole variants are not unheard of). Proper hole fitment on end blocks is a careful balancing act: put too much space between the two holes and the rollers will grab too much meat, ruining it for production; place the holes too close together and the subsequent friction will quickly wear down your rollers, aging them prematurely.
That said, while ineffective blocks can waste time and product yield, end blocks that are in good shape, bolted down squarely and level, can give your existing rollers a longer lifespan and increase overall peeling productivity simultaneously.
Roller Bushings
Brass bushings are fitted onto each shaft of the roller when it is put into end blocks. As such, the bushing is the contact point for the poultry peeling roller and the peeling machine itself. Bushings also provide extra lubrication so that rollers can spin more freely and preventing miscuts from snagging or friction.
However, like any other piece of equipment, roller bushings don’t last forever, and high workloads can quickly wear them down. Once bushings start to wear, their reduced effectiveness can start opening up space between rollers, leading to miscuts and all sorts of other potential problems.
Well-fitted, tight bushings will help both your rollers and end blocks last longer and reach higher yields. Just remember that, like blocks, failure to inspect and maintain existing bushings can lead to big problems in the long-term.
Why It Pays To Invest In Great Blocks And Bushings
For many poultry plant managers, keeping up-to-date on blocks and bushings is the single most cost-effective way to get a longer effective lifespan out of their existing rollers. This is caused by multiple factors, but the biggest is upfront costs for blocks and bushings when compared to replacing the rollers themselves, or even the entire peeling machine.
For a cost comparison, while a new set of rollers can cost over a hundred dollars depending on the manufacturer, bushings can be replaced for about two dollars a piece. With the efficiency and yield gains that new bushings can provide, their low price point means that savvy plant managers can keep the same roller set on the line for days longer without having to shut down.
Block and bushing upkeep is also a huge consideration for plants running older machines that are difficult or impossible to find replacement rollers for. While managers will still eventually have to upgrade their machines or find a custom roller manufacturer, simply switching out blocks and bushings can be a great way to push machines that much further when deadlines are looming.
The takeaway: if you’re looking to keep your poultry peeling machines lasting at maximum capacity for as long as possible, don’t forget about the blocks and bushings!
For more information about poultry peeling rollers, how they work, and how you can get the most out of the rollers in your poultry plant, download our free informative guide, The Lifecycle of a Poultry Peeling Roller, and start making gains at your plant today!