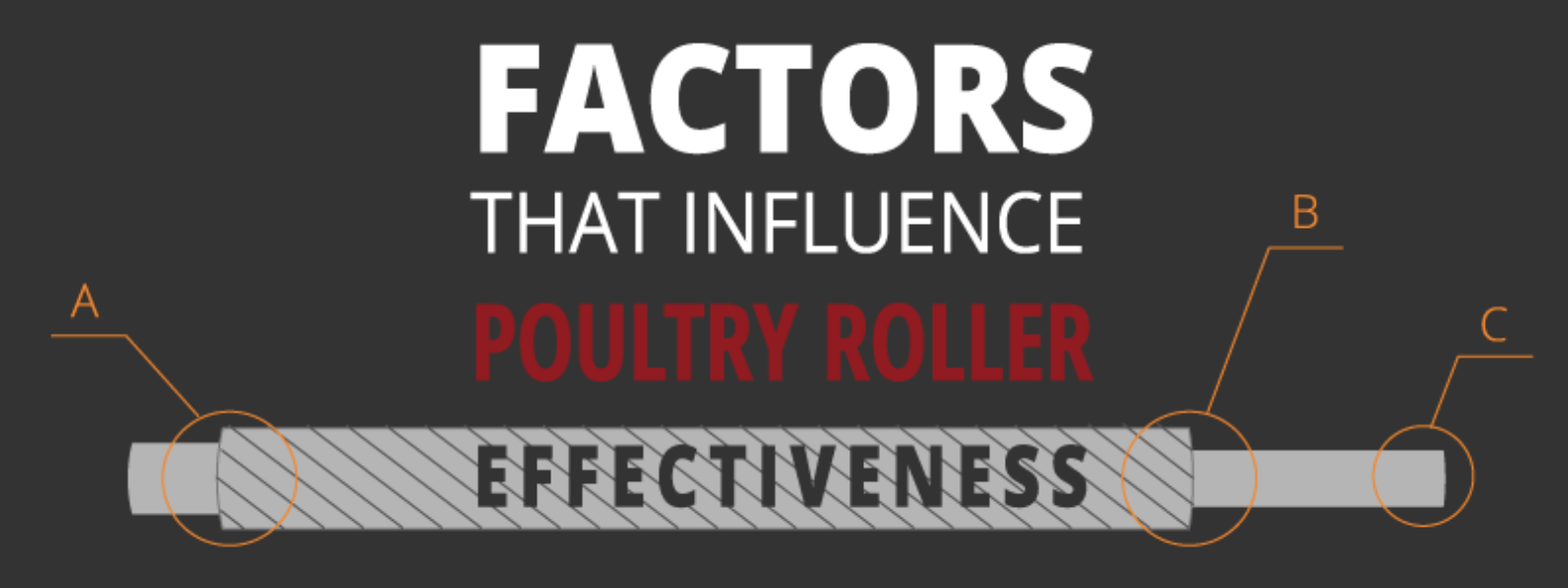
17 Oct Factors that Influence Poultry Roller Effectiveness
Rollers are a vital part of the modern poultry production process, used for peeling away and eviscerating gizzards, breasts, and other areas of the bird that must be removed before processing can be completed. However, not all poultry rollers are created equally, and effectiveness can vary wildly based on the make and condition of the roller in question.
Read on for some of the most important factors affecting your poultry rollers, and some warning signs to be on the lookout for if it’s nearing time for replacement.
Teeth
The first and most obvious factor impacting a roller’s performance is the sharpness of its inter-engaging helical teeth. A roller’s teeth will gradually get worn down after continued use, drastically degrading its effectiveness. Eventually, a roller’s teeth may be degraded to the point that they can no longer cut through a bird’s skin and membranes, at which point the roller will need to be refurbished or replaced.
Shaft
While the shaft of the roller isn’t directly responsible for peeling or evisceration, a roller with a degraded or poor-quality shaft won’t be able to spin properly, which can in turn cause miss-cuts or other damage to the bird. If a worn shaft is holding your roller back, don’t hesitate to find a suitable replacement.
Material
In addition to individual components like the teeth and shaft that can get worn down over time, it’s also important to take each roller’s overall material construction into account.
In most cases, rollers will come in one of two materials: tool steel or stainless steel. While there generally isn’t a difference in lifespan between the two materials, stainless steel rollers are about $38 more expensive per pair than their tool steel counterparts but make up the difference with increased protection against aging and rust. Choose wisely.
Action (Automatic vs Manual)
A roller’s productivity is also affected by whether it is intended for automatic or manual use. While poultry production as a whole continues to become increasingly more automated as time passes, many plants still operate using manual rollers, and each type has its associated pros and cons.
Because they work at a steady pace without fluctuations, automatic rollers produce a more predictable yield at an increased processing speed over manual rollers. And because automatic rollers don’t come into contact with human hands, they present a lower chance of contamination, worker injury, and other safety hazards.
On the other hand, while automatic rollers can process birds faster, manual rollers allow skinned birds to be reworked without further damage, resulting in a higher-quality final product. Manual rollers aren’t as prone to over-processing of products, and are also generally easier for employees to reach than automatics, consequently making them easier to clean and maintain.
Age
No matter how well-maintained, every piece of equipment at your plant will eventually succumb to the passage of time. Whether it be depleted functionality or obsolescence in the wake of new technological breakthroughs, knowing when to replace parts in your plant that have been in use for too long is essential to maintaining peak performance.
Rollers are no exception, and a roller’s age is generally the deciding factor for how well it will perform. The industry-standard lifespan for poultry rollers is 6-8 weeks; plants can expect to see overall yields drop by as much as 10% for every week after this period that the roller remains in use. Keeping your rollers clean and well-maintained can increase their effective lifespans, but keeping the same rollers in rotation for over 8 weeks is asking for trouble.
Want to learn more about poultry rollers, and how you can make the most of the ones in use at your poultry production plant? Check out our free informative guide, The Lifecycle of a Poultry Roller, and start getting more out of your plant’s rollers today!