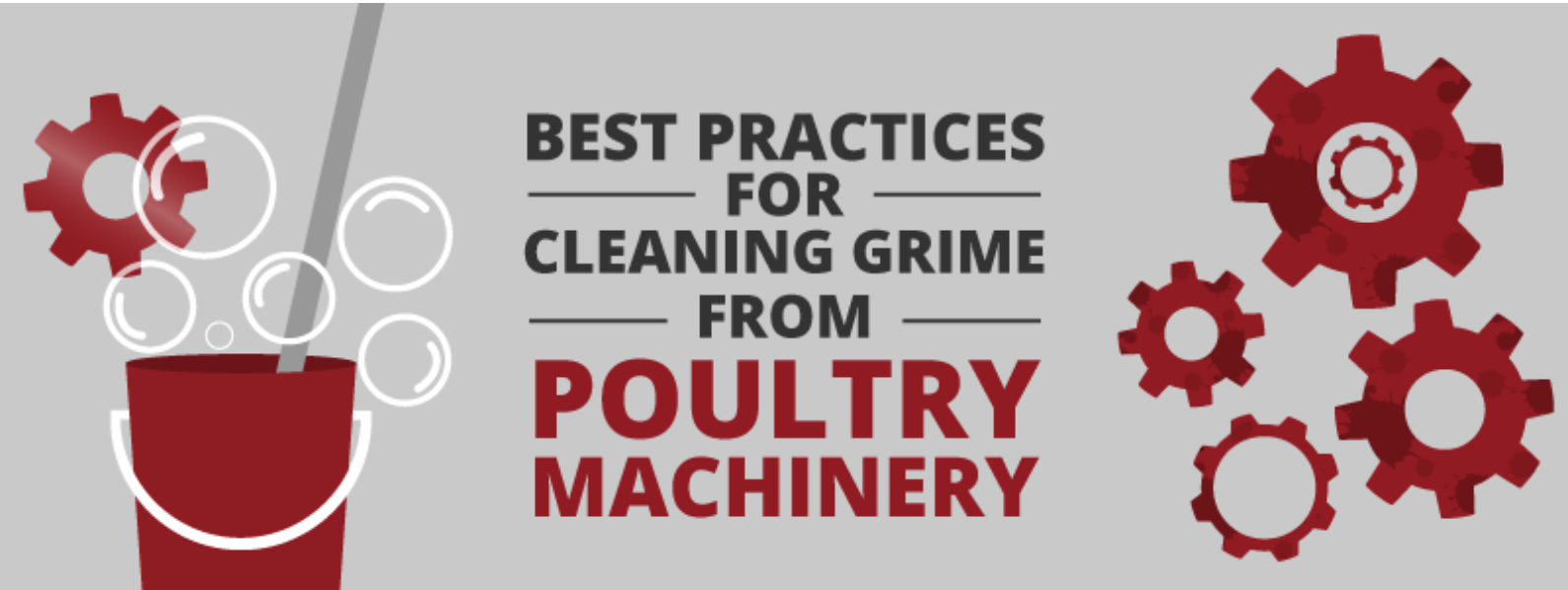
18 May BEST PRACTICES FOR CLEANING GRIME FROM POULTRY MACHINERY
In any industry, machinery breakages can cause huge monetary losses, but the danger is never greater than in the food processing industry. Beyond money lost from downtime, a poultry plant with broken machines can see missed deadlines, inferior products, and potentially disastrous recalls.
One of the biggest reasons that machines break is due to dirt and grime buildup. Without proper procedures in place to care for and maintain the machinery and equipment that keeps the plant up and running, something is bound to break eventually, so keeping everything clean should be a top priority.
Here are a few best practices for keeping machines clean, healthy, and running at maximum efficiency.
Seals, Filters, and Breathers
Most heavy machinery is comprised of a number of moving parts and sections. These sections are segmented from one another with seals and filters designed to keep contaminants from moving from one part of the machine to another.
As part of regular scheduled maintenance, place particular emphasis on your machines’ seals, filters, and breathers (Apriso). Inspect seals regularly to ensure they’re in proper working order, change filters at regular intervals to mitigate any dirt or contaminant buildup, and keep breathers clean to avoid creating a vacuum that can suck contaminants into the vulnerable inner workings of the machine.
Machinery Dismantlement
The bigger the machine, and the more moving parts, the higher the probability that a once-over with a pressure washer just won’t cut it. There are often parts hidden from view that can’t be reached while the machine is assembled, meaning that a conventional cleaning will only allow grime to build up in its inner gears and parts.
While it may not be necessary for every piece in your plant, don’t be afraid to dismantle one of your machines in order to deep clean and inspect every last moving piece (Daimer) . For the best results, stagger machinery dismantlement so that other machines can make up for the lost productivity of the one being deep-cleaned.
Gear Lubrication
Unlike friction materials, seals, and gaskets, gears and shafts do not break down as often and can go for a much longer period of time before being replaced. However, just because they’re still working doesn’t mean they’re not collecting contaminants that can clog up other processes.
As another method of protecting yourself from breakdowns, ensure that all the gears on your machines are well-lubricated so that they can move without grinding or snagging on other parts of the machine. Lubricated gears present less potential for parts to get caught or for dirt and dust to settle, meaning that the machine as a whole will be at less risk for an accident. The same holds true for bearings and shafts.
Contamination Prevention
There’s a reason why car enthusiasts keep their cars in the garage or under a cover: nature is a brutal thing to machines. It may take time, but any machine exposed to heat, rain, wind, and other weather will eventually have its parts rust, rot, and break down, so it pays to keep your equipment as insulated as possible.
The less your equipment is exposed to the elements, the better. In addition to the seals on the machine itself, check the seals on the doors, windows, and other openings that exist on your factory floor. The more airtight you can make your factory, the longer your machines will last.
For more great strategies you can use to push your machinery further, download our free Ebook, Why and How to Cross-Train in Maintenance, and take your poultry plant to the next level today.