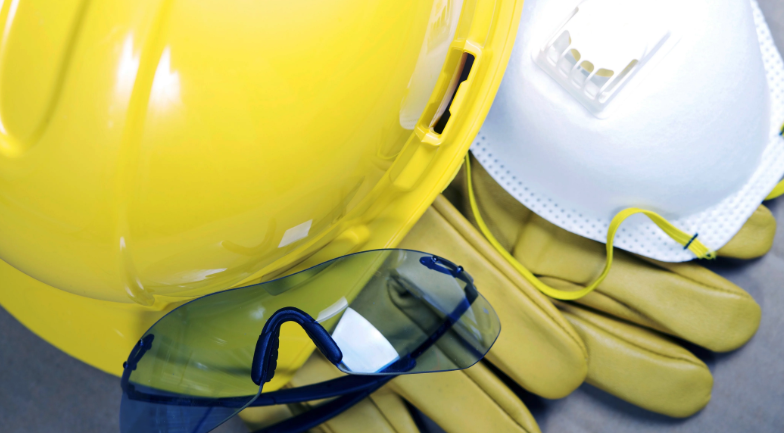
28 May Understanding Machine Guards
Safety should be the most important thing in every workplace. There are far too many unguarded or inadequately guarded machines that employees are exposed to daily in workplaces throughout the country. At Delong’s, we want to stress the importance of properly guarding your machinery and keeping the safety and general well-being of employees top priority.
What to Guard?
Machines in the poultry processing industry are highly specialized and necessary for production. They require proper instruction and safety measures to be used. Machines must be guarded if there are hazards related to point of operation, ingoing nip points, rotating parts, flying chips, and sparks. If there is not a possibility to attach the guard to the machine, it must be attached to surrounding areas and ensure machine cannot harm an employee.
According to OSHA, the following machines also need to be guarded at all times:
- Guillotine Guards
- Alligator Shears
- Power Presses
- Milling Machines
- Power Saws
- Jointers
- Portable Power Tools
- Forming Rolls and Calendars
- Barrels Drums
- Blades
Anchoring machinery so that it cannot move or harm an employee is essential to maintaining a safe working environment. Without recognizing these hazards, they cannot be addressed. Guarding machines, staying alert to hazardous conditions and listening to employee concerns are all essential elements to a safe workplace.
Why Do Machine Injuries Occur?
Machine guarding is one of the most important things to consider when working with heavy and dangerous machinery. Even when applied, injuries still occur. Here are some of the most common ways these injuries take place:
Pressuring Demands – When employees are pressured to increase their work pace and rate of production, they may remove the machine guards. Production incentives may also cause workers to take a faster, but riskier approach.
Old Machinery – New machinery is often designed with guards built in to the construction of the machine. However, older machines need to be retrofitted with guards. Unfortunately, many factories and production plants keep using their old, outdated machines until they no longer work properly; this poses many safety threats in itself. If a machine is too old to be fit with guards, look for alternatives to safeguard it.
Adjusting and Fixing – If a machine has a problem that needs to be adjusted or fixed, the guards are likely to be taken off during maintenance. The guards must be replaced after maintenance is done to the machine to ensure safety of workers. If not replaced, workers will be exposed to dangerous parts of machinery.
Jams – If the production line, or a specific machine jams, make sure to completely turn off the machine before working on unjamming it. Employees often remove or bypass guards to clear the jam, and if the machine isn’t properly disabled it could recommence its action when you’re in a danger zone.
Cleaning – When a machine needs to be cleaned, guarding is often removed for adequate cleaning. The machine guards should always be put back on immediately following the completion of sanitation.
How Can Proper Management Help?
Production speed is important, but employee safety is more important. Management should never encourage workers to cut corners on safety, in order to produce at a faster rate.
Employee’s should be properly trained on how and why machine guards are used. They should be trained to:
- Identify, describe, and recognize potential hazards associated with the machine
- Understand the type of guard they will be working with and how it protects them from danger
- Know when to, how to, and who can remove the guard on their machine.
- Know what to do if a guard is damaged, missing, or not working to its full efficiency.
- Not take independent action in machine guard related matters, and to involve supervision if necessary.
Understanding what it takes to create a safe work environment is the first step to having one. For further safety education and tips on creating a safe workplace, check out our latest free guide, Poultry Plant Safety Checklist.