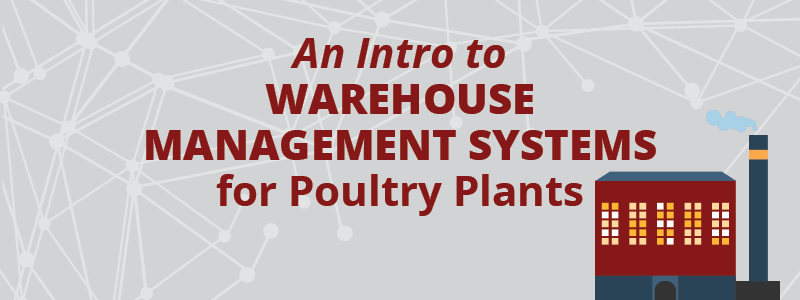
07 Sep An Intro To Warehouse Management Systems For Poultry Plants
Regardless of industry, efficiency is always key when it comes to doing business. No company can make money if its employees are unorganized, overworked, or constantly making errors, so managers are always on the lookout for ways to improve on these areas.
If you’re a poultry production plant manager and have found yourself in a similar situation, a potential solution exists in the form of a warehouse management system. What is a warehouse management system, and how can it help managers at their plants? Read on for more information.
What is a Warehouse Management System?
A warehouse management system (WMS) is a software-based system designed to help managers as they oversee the logistics and day-to-day operations of their facilities. As the name implies, warehouse management systems see heaviest use in the warehouses and distribution systems of the companies that employ them.
The Association of German Engineers defines a warehouse management system as, “…the management, control and optimization of storage and distribution using a software system (including storage and storage management, as well as the management and administration of the equipment), with extensive methods and means for checking the system conditions and with a selection of operational and optimization strategies. The task of a warehouse management system (WMS) is to manage and optimize in-house storage and transport systems.”
After installation, the WMS takes over the responsibility of controlling and optimizing all of the complex warehouse and distribution systems that keep the plant up and running. Managers can then monitor their facilities’ entire material flow all from one central display, boosting their productivity and allowing them to move from task to task more quickly.
However, while even the basic core functions like volume and stock management can be godsends to deadline-driven managers, the real strength of a warehouse management system comes from its more-complex processes. Subcontracting, shipping, and picking can also be streamlined through a WMS, simplifying processes that were once logistical nightmares.
How a Warehouse Management System Works
A properly-integrated warehouse management system will act as the central unit in the facility’s software structure. After receiving orders from the overlying host system, the WMS enters these orders into a database, organizes them, optimizes each process, and then sends each order to the appropriate conveyor system.
A modern WMS oversees all intralogistic processes going on throughout the plant, all the way from initial raw material delivery all the way to shipping the finished product. Every process is documented and catalogued so that managers can fix problems as quickly as they arise and gradually tweak their processes until peak efficiency is achieved.
WMS optimization allows poultry plants to operate closer to peak efficiency. With everything optimized, fewer products sit in storage, fewer resources are required to get a bird fully processed, and fewer personnel are needed to deliver finished goods to customers.
Four Key Ways Warehouse Management Saves Money
Better Productivity
According to a report published by Georgia Institute of Technology’s School of Industrial Systems Engineering, distribution centers spend about 50% of their labor hours traveling between transactions, about 30% completing paperwork, and only about 20% of their time actually handling materials.
With a WMS, these wasted hours are a thing of the past. Task prioritization can drastically reduce employee travel time and paperwork, giving them more time to focus on the bottom line. A WMS can also be used to predict how many employees will be required to complete a given task, allowing managers to save on labor and allocate their human resources more effectively.
Fewer Mistakes
WMS incorporates scan confirmation, significantly cutting down on the types of careless mistakes that result in huge losses due to downtime or product recalls. Because it records every process that goes on throughout the plant, a WMS gives managers the ability to automate their filing system and reduce their paper use – or eliminate it entirely.
WMS means fewer mistakes get made, and fewer mistakes means more customers leave satisfied and confident to buy your product in the future.
Detailed Analysis
With detailed records of the past comes detailed analysis so that you can prepare for the future. Reporting tools display which areas of the plant are performing to standard, which ones are outperforming expectations, and which ones need immediate attention, allowing managers to react accordingly.
Among other benefits, detailed analysis takes a lot of the guesswork out of a manager’s job, especially in the realm of business development. If you’ve been considering expanding your operation or changing stocking practices, now you’ll have concrete data to help you decide the best next step.
Increased ROI
Of course, no other benefit matters in the long run if it doesn’t extend the bottom line. Fortunately, a well-implemented warehouse management system presents ample opportunities for managers to save money and increase their ROI as they streamline their plant’s processes.
Naturally, more productive employees making fewer mistakes results in better returns, while detailed metrics allow managers to tweak their processes to emphasize their strengths and mitigate their weaknesses. The bigger the operation, the more pronounced the effect, and bigger plants with larger inventories will see huge cuts to travel time and other waste.
If you’re interested in getting a WMS for your plant and want to explore your options, search around for comparison sites for warehouse management system buyer’s guides.
And if you want to revitalize your poultry plant by implementing better, more efficient systems, you can learn more about how to do just that by downloading our free informative guide, How to Find Efficient Poultry Processing Equipment. Take your plant to the next level today!