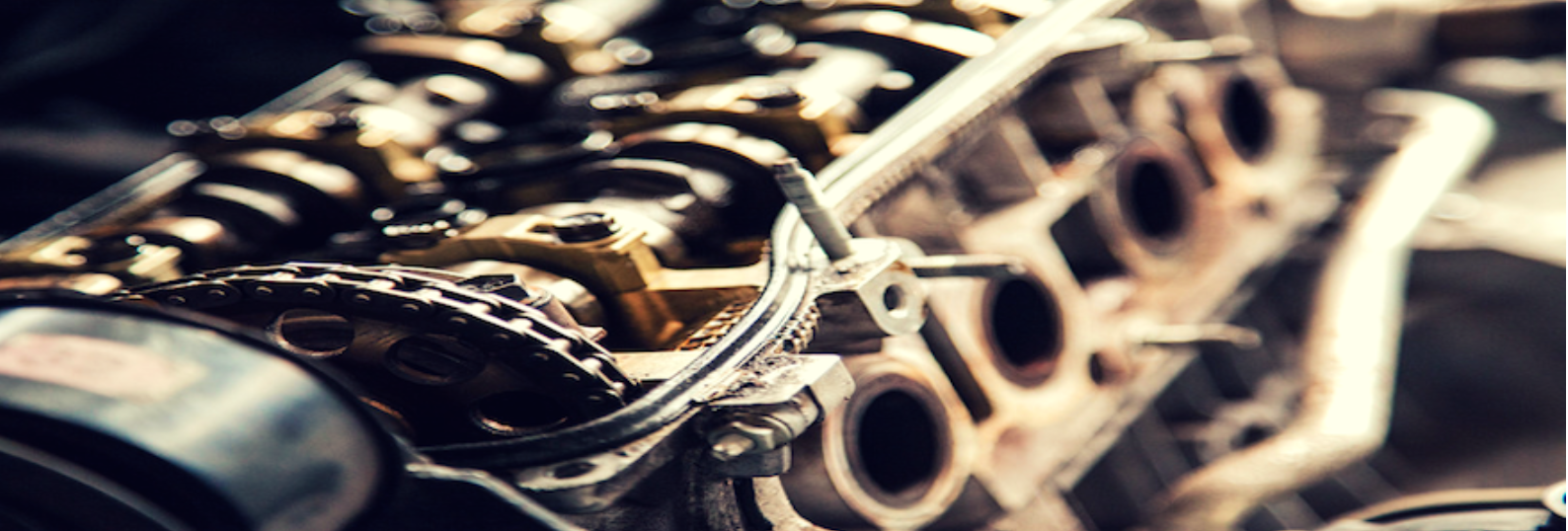
20 Feb How To Do A Spare Parts Analysis For Your Poultry Plant
In order to minimize downtime caused by a machine breaking or malfunctioning, poultry plants should have spare parts on hand to make repairs quickly. But parts can be expensive. It’s incredibly important to know what parts your plant needs to have on hand and which ones you can do without. In order to achieve this, you will have conduct a spare parts analysis. This article will show you 4 critical steps to conduct a spare parts analysis to save money and reduce downtime (LCE).
Step 1: Develop An Equipment List Including All Maintainable Items
Before determining which spare parts you need to stock, it is important that you first identify all of the repairable equipment in your facility. You can organize this list in an easy to read spreadsheet with data generated by a Computer Maintenance Management System (CMMS) with an asset index, or Enterprise Asset Management (EAM). This will enable you to assess the equipment on site and make quick decisions regarding stocking.
Step 2: Analyze The Importance Of Each Item
Once you have generated a list of your maintainable assets, it is essential that you run a criticality analysis on each individual item. This analysis should take into account the overall importance of an asset and use a Failure Mode Effects Analysis (FMEA) to determine the frequency and consequence of product failure. Each of these processes can be used periodically throughout the life of each piece of equipment. (Reliability Web)
You must also identify the risk associated with product failure. Make sure and assess the associated safety, environmental, and stakeholder risks. It’s important to convert the consequence of risk into a potential financial impact on the company. Note that having the right parts on hand will help manage the negative impacts of a breakdown, working as insurance.
Step 3: Assess Product Delivery, And Repair Time For Each Item
After determining the value of each item, you may create a chart or list ranking the items and the required lead time for spares. This will enable you to determine exactly which items you need in-house. In doing this you must also assess the delivery and repair time for each piece of equipment and relevant parts. By knowing exactly how long it will take to ship the parts and repair each item you will be able to stock the optimal amount of spares, reducing holding costs and saving space.
Step 4: Determine A Course Of Action
Once you have developed a list of your assets, analyzed the importance and risk of failure for each one , and determined which parts you neeed in-house, you must finally determine a course of action. Make sure to work with your suppliers when determining which parts to have on hand. You made be able to set up a vendor agreement to supply a part within a specific time frame, or possibly provide you with equipment on consignment, which you would hold without cost until you use it.
If you follow these steps carefully you will be able to effectively save money and downtime by having the proper parts on hand, and have an organized system for stock management to ensure that you have the right parts when you need them (Reliability Web).