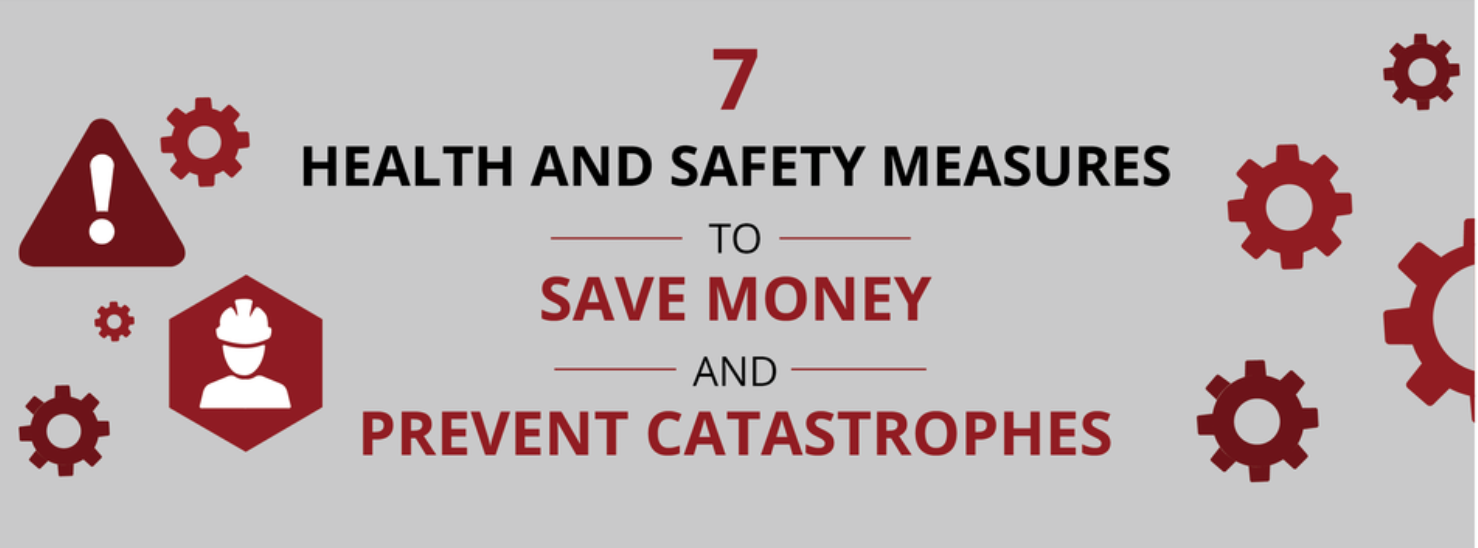
13 Jul 7 Health and Safety Measures to Save Money and Prevent Catastrophes
Working in a poultry processing plant can pose a number of health and safety risks for employees. However, there are measures that can be taken to manage these risks and prevent unnecessary, expensive, and potentially dangerous catastrophes.
Provide Protective Equipment
Personal protective equipment is any form of equipment that helps minimize exposure to risk in the workplace.
For meat processing plants, common protective equipment includes basic skin covering (gloves, safety goggles, earplugs, coveralls, vests, hard hats) as well as specialized gear (respirators, full-body suits) designed to protect workers from other hazards, particularly airborne pathogens.
Employers must supply each employee with the necessary equipment for their role so that they can accomplish their everyday tasks as efficiently and safely as possible.
Likewise, managers have a responsibility to teach every worker under their supervision how each piece of equipment works, common mistakes to avoid when using it, and how to properly clean and maintain it.
Create an Effective Ergonomics Program
Workers in the poultry industry are often assigned tasks that can damage their muscles, nerves, blood vessels, ligaments and tendons.
Employers can manage these risks by outlining and clearly communicating their goals for the ergonomic process and involving their front line employees in identifying the risks they face on the job.
Once risks are outlined and solutions to control all potential hazards are in place, it is then necessary to provide adequate job training to employees, as well as encouragement to report any early symptoms of work-related medical problems they may be experiencing.
The ergonomic process should be ongoing and progress should be evaluated frequently to manage any hazards that may pop up later and to evaluate the effectiveness of measures that have been taken.
Implement an Effective Hearing Conservation Program
Noise is one of the most common occupational hazards facing industrial workspaces, as extended exposure to loud noises can cause long term damage and even permanent hearing loss.
To keep their workers safe, employers need to monitor all employees exposed to noise levels above 85 decibels for over eight hours a day, and provide them with hearing protection.
Control Hazardous Energy Sources
Hazardous energy sources can include, but are not limited to,electrical, mechanical, chemical, or thermal energy from machinery.
These types of hazards can appear unexpectedly during service and maintenance, particularly when a piece of equipment is first started up, putting unprepared workers at risk.
To help curb potential workplace injuries, workers who perform maintenance and servicing tasks should be instructed to always make certain that all equipment is shut down before performing their tasks.
Create an Accident-Proof Workspace
Beyond special training for workers that regularly operate dangerous machinery while on the job, equipment should also be modified to be as safe as possible for the operator.
Safeguards like a tapered throat or a fixed guard for meat grinders prevent simple solutions to increase the relative safety of the plant without sacrificing overall product yield.
Accident proofing also extends beyond the product itself. Incorporate caution signs, safety instructions, and hazardous materials warnings liberally, and inform all workers about the potential dangers they could face if they choose to ignore these warnings.
Sanitize Everything
In order to protect workers from biological hazards, such as salmonella and other diseases, you’ll need to set and maintain workplace cleanliness standards for each piece of equipment, the processing plant as a whole, and for individual employees.
Proper ventilation must also be in place, both tohelp control airborne contaminants, and to prevent life-threatening accidents like fires and explosions from happening.
Maintain Proper Workplace Safety
All surfaces at the plant should be cleaned and maintained properly. Clean countertops, tables, and shelves lessen the risk of valuable materials being dropped or tipped-over, while clean floors help prevent workers from slipping or falling while on the job.
Likewise, doors and emergency exits should never be blocked. Every employee on the floor should be able to open any exit doors without the need for keys or tools so that they can safely evacuate should a hazardous situation arise.
Want to learn more about how to save money at your plant without sacrificing safety, efficiency, or product yield? Download our free informative Ebook, Why and How to Cross-Train in Maintenance, and start taking your plant in a new direction.