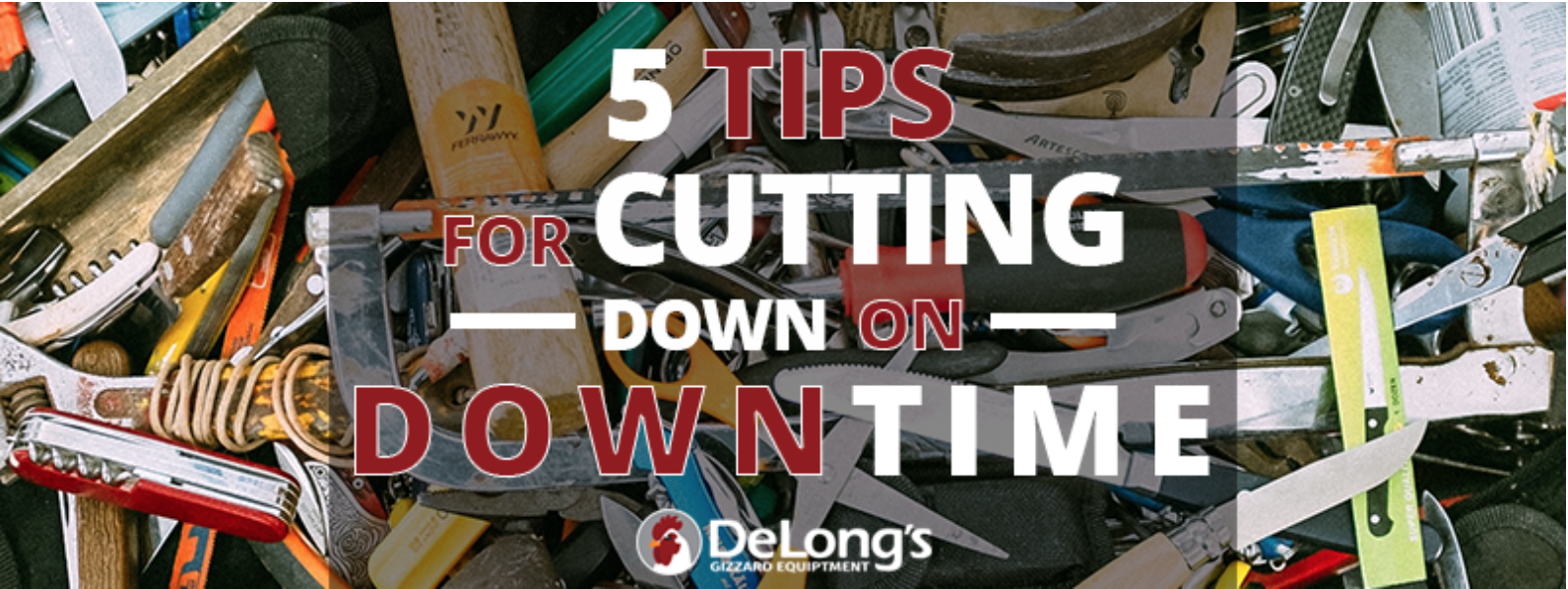
22 Jun 5 Tips for Cutting Down on Downtime in Poultry Plants
For poultry plants and other meat processing facilities, downtime can be described as any time not being productive. Downtime can be caused by a number of factors, but most of the time, it stems back to improper employee produces or machine failure.
While a great maintenance team can be instrumental in decreasing plant downtime and increasing overall productivity, there are a number of steps managers can take to keep their plants running longer and more effectively. Most of these steps are not mutually exclusive, and combining them effectively will allow you to identify any issues, create a plan of action, and implement it quickly.
Motivate Your Maintenance Team
Maintenance can be a tough job. Oftentimes, the production team gets the credit when things go right, while the maintenance team takes the blame for anything that goes wrong. This can lead to low morale and, consequently, an unmotivated and apathetic maintenance team.
Keeping maintenance team morale and motivation high can go a long way in keeping your plant moving at maximum efficiency. Having motivated maintenance workers that take pride and ownership in their work, and who are rewarded for their efforts, will go the extra mile to keep problems from happening. Before you take care of your equipment, take care of your team.
Remember that motivation can take many forms, and that it’s your responsibility as a manager to instill a sense of purpose in your team. Start by setting realistic and obtainable goals, giving individual praise for good work, offering bonuses for reaching certain goals, and using any other methods you can think of to incentivize, rather than punish, each member of your maintenance team.
Keeping morality high is a challenge for any manager, but those that can inspire their maintenance workers to give 100% will see better, more productive plants in the long run than any new machine or equipment can provide.
Track And Categorize Downtime
Be aware of where in the production process your plant is experiencing downtime. Once you’ve identified problem areas where your plant could be more productive, you may realize that what appears to be a big problem has a simple fix.
Even if there are several difficult steps to decrease downtime in a specific area, knowing how to quickly identify and localize an issue is the a key step in keeping the process of fixing it manageable.
Once you have identified your plant’s key areas of downtime, categorize your downtime issues by the cause. In addition to keeping things more manageable for the maintenance team, categorizing issues that arise can both help you uncover some larger issues within production as well as implement plant-wide fixes that can potentially alleviate multiple problems simultaneously.
Keep Your Maintenance Team On A Schedule
Even the smallest issue, such as dirt in the grooves of a machine, can cause a costly breakdown. With so much at stake, having strictly-scheduled regular maintenance is a necessity.
Give your maintenance team a schedule that breaks down specific tasks and timelines of the general maintenance procedures needed to keep your equipment moving. Be sure to assign specific team members to specific tasks to avoid any “I thought someone else was going to do it” situations.
A scheduled general maintenance routine can also give you the benefit of identifying potential problems before they start. After all, it is much easier to predict a problem when your maintenance team is familiar with your equipment and regularly working with it.
Encourage Communication
Open communication across teams can make it easier for downtime to be quickly identified and fixed.
Encourage your operations team to talk directly to your operations team about any malfunctions or potential problems the equipment may be facing. With proper two-way communication in place, the essential messages get to the problem-solvers and nothing is lost in translation between the two teams.
Open communication between maintenance and management should be encouraged as well. When something goes wrong, managers and maintenance should feel comfortable to discuss the problem and decide the best course of action. Keep the maintenance team involved in the decision process will also make them feel valued and encourage their active involvement.
Conduct Regular Employee Evaluations
If you believe that most of your downtime stems from your employees, conducting regular employee evaluations can identify those who are using improper procedures, falling behind, or not using their time efficiently.
One effective method of evaluating employees is a 360° Performance Evaluation. This method of evaluation requires every person or department that the employee interacts with to submit reviews on their performance, including management, operations, and other maintenance workers.
The 360° Performance Evaluation can be effective for decreasing downtime in maintenance because it can bring up issues that management would not normally see. Having workers from other departments comment on what they see can give management a better, fuller of each employee’s capabilities, what they bring to the plant, their strengths, and what needs improvement.
The maintenance team keeps poultry plants up and running, and the best maintenance workers need the right training, motivation, and oversight from management to reach their full potential. For more information about training your workers can lead to better yields and more efficient processes, download our free Ebook, Why and How to Cross-Train in Maintenance.