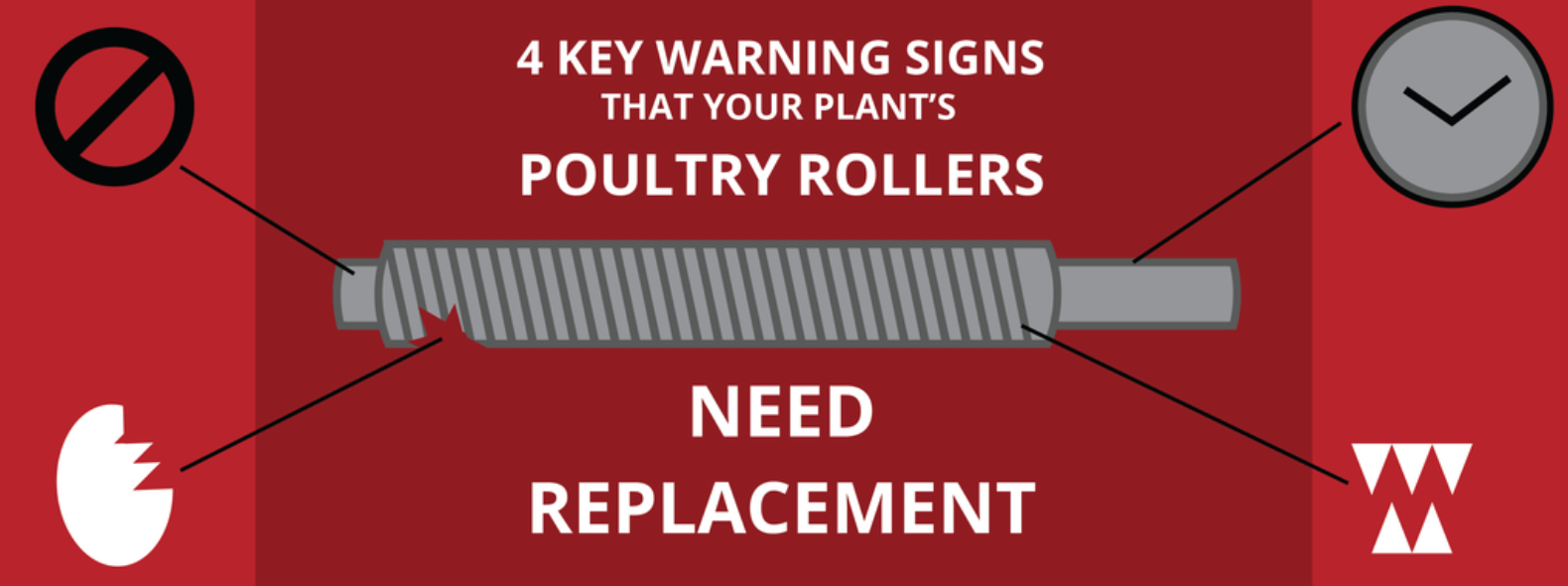
23 Oct 4 Key warning signs that your plant’s poultry rollers need replacement
It’s understandable for poultry processing plants to strive to get the best yields possible about of their poultry rollers. Through careful cleaning and maintenance, managers can give their rollers the longest effective lifespan possible – but that’s not always enough.
No roller lasts forever. No matter how well-maintained, every poultry roller at your plant will eventually need to be replaced. For many managers, the biggest problem is knowing when to replace: most rollers will last 6-8 weeks, but certain factors can prematurely age a roller to the point of ineffectiveness.
Here are a few warning signs that it might be time to get a new set of poultry rollers:
Signs You Need To Replace Your Rollers
1. Fat And Skin Buildups
If you notice a buildup of fat and skin on your rollers, it means that they aren’t doing their jobs properly and aren’t effectively cutting through the skin and membranes on the bird.
Keeping rollers free of this buildup can go a long way in increasing their longevity, so inspect all of your rollers thoroughly for any signs of buildup. If you find any offenders, take them out of commission until you can replace them with new ones.
2. Broken or Depleted Functionality
Although rollers typically have a lifespan of 6 – 8 weeks, complications can arise from vibrations, shock, or high temperatures. From time to time, these factors can cause a roller to age prematurely, costing them efficiency and potentially depleting their functionality entirely.
If your rollers aren’t performing as well as they should be based on their age, your best options are to see about having them refurbished or, if the damage is too great, replacing them entirely.
3. Outdated Equipment
As advances in the poultry industry are made, better and better rollers make their way onto the market. Even if your rollers are producing solid yields, there is always the potential for better productivity – and even if you aren’t pursuing it, your competitors might be.
Stay up to date on the latest trends and breakthroughs in the industry, and if technological innovation makes your current equipment outdated, don’t be afraid to make an upgrade.
4. Dull Teeth
When it comes to poultry rollers, worn teeth cause more issues than any other factor. If the teeth are worn down, they can’t peel and skin poultry effectively, and miscuts can damage the bird and even make it unfit for consumption.
Start by looking for pits in the peel. If there are more pits in the teeth than can be fixed, seek a replacement as soon as possible. If the pits are over one-fourth inch of the teeth depth and cover more than 25% of the overall surface area of the peel, then the roller is worn out and needs to be replaced.
Other Areas To Inspect
Rollers are far from the only part of your plant subject to deterioration over time. However, certain factors, such as the roller blocks and bushings, can indirectly affect the yield if they are left on the peeling machine for too long without replacement.
Blocks and bushings should be cleaned on a routine basis, but they will still break down eventually. Bushings should be replaced about every two weeks and blocks should be replaced every four months.
Predictive Maintenance Techniques
Although roller replacement and installation can be a hassle, there are methods to detect breakdowns in your equipment before they occur. In the poultry production setting, effective predictive maintenance requires employees to routinely check issues like fat and skin buildups, dull teeth, etc. and identify problems before they arise.
Fortunately, technological advancements in the industry have provided managers with a number of ways to detect issues before substantial equipment damage can occur. Two of the best methods are:
- Vibration Analysis: Machine parts emit different vibrations depending on how worn out they are. Handheld vibration monitors or monitors built into the equipment can inform your plant when a roller is beginning to deteriorate.
- Thermal Imaging: When a part is being worn down or there is a circuit malfunction these areas will emit extra heat. Thanks to thermal imaging technology, you can now detect these areas and take proper action to repair them.
At the end of the day, every roller will at your plant will eventually need to be replaced. Fortunately, knowing the warning signs of a breakdown and using preventative maintenance technology can cut replacement costs and eliminate downtime simultaneously, so always be on the lookout for ways you can introduce preventative maintenance practices to your plant.
If you’re looking for more information about what makes a great poultry roller, and where you can find them, download our free informative guide, Lifecycle of a Poultry Roller, and start getting better yields from your poultry processes today.