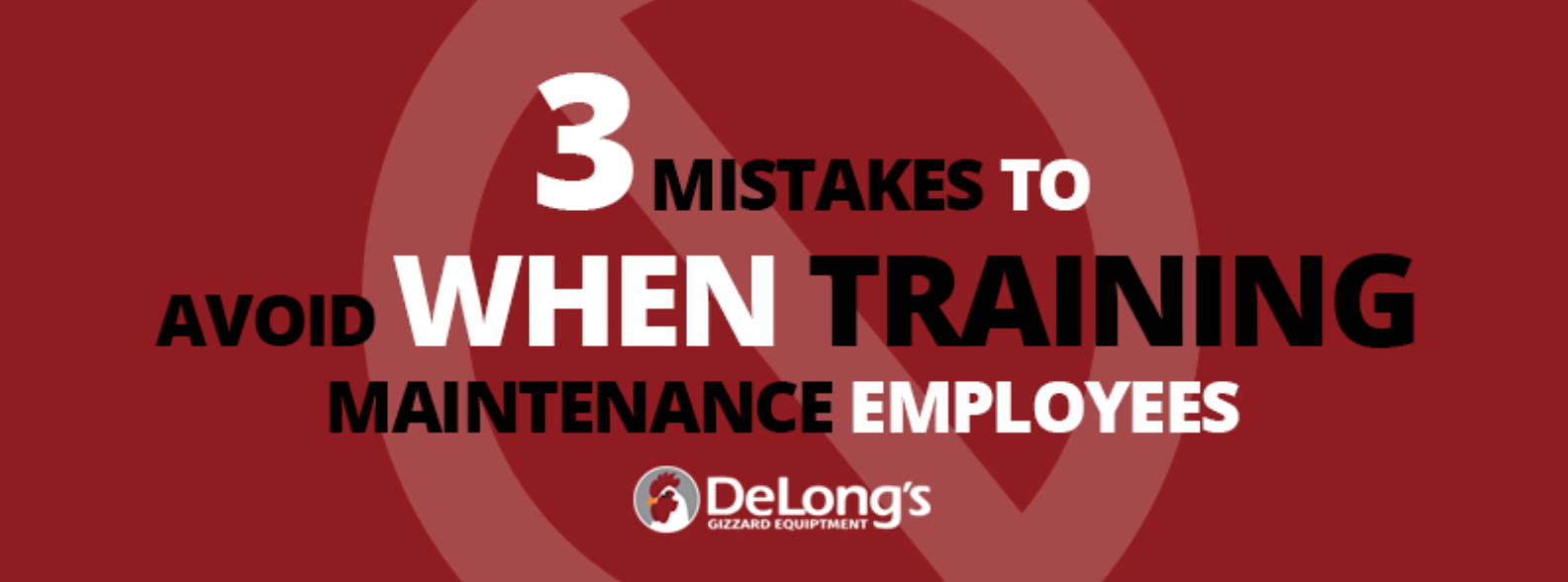
29 Jun 3 Mistakes to Avoid When Training Maintenance Employees
While proper training is essential to effective plant operation, mistakes when training employees can have a devastating effect on the plant in the long term. Improper training can lead to workers developing bad habits that can be ineffective, wasteful, or even dangerous.
This problem becomes even more apparent in the realm of maintenance. The maintenance team serves a crucial role in keeping the plant up and running, and managers can’t afford to leave their plants in poorly-trained hands.
Here are three common mistakes to avoid while training maintenance employees:
Rushing
Be thorough in your training. Maintenance keeps your business running smoothly, so make sure your maintenance team is prepared for any breakdown, spill, leak, or hazard. Anything can happen, so make sure your team can handle any situation well.
It is important to teach each maintenance employee not only what each machine does, but also its role in the grand scheme of things. That way, if several malfunctions occur at once, your maintenance team will better-equipped to prioritize their task list efficiently.
Do not let your employees feel like they are being left in the dark. Competent employees are often the most motivated, and providing your maintenance team with a comprehensive education about their role will build their confidence in their own abilities.
Neglecting to Record Results
Recording results allows you to see the efficiency of your current training program. By testing and analyzing the results of each training session, you’ll be able to see what works and what doesn’t, allowing you to gradually develop and improve your training program to best suit your team.
First, strict recordkeeping will allow you to measure the efficiency of your training program. By recording the results, you’ll be able to get a bird’s eye view of what went well in training and what needs to be improved. Make sure to set specific, quantifiable benchmarks to effectively measure results.
Second, recording everything allows you to better track the progress of individual employees. In addition to the team as a whole, keep uniform benchmarks that every maintenance employee should be able to meet. These will help you identify which employees need more training, and in what areas.
Lastly, recordkeeping will allow you to oversee the entire maintenance department and identify what is not getting done. For example, by looking through records, you could find that a certain area is always dirty because the maintenance employees were not informed that it needed to be cleaned.
During training, be sure to teach proper recording procedures to each team member, and stress the importance of accurate records.
Making Training a “One and Done” Deal
No matter how great the teacher, a student won’t be able to learn effectively if the information is presented only once. As you teach and train your maintenance team, remember that training is an ongoing process, evolving and changing over time but never stopping.
Maintenance employees should have periodic refresher courses on proper safety practices. This will keep team members keep workers from developing any bad habits and stop them from becoming complacent from doing their procedures so frequently.
In addition, the entire team should be extensively trained any time new equipment is introduced. Leaving an employee to figure out how a machine works without proper guidance is asking for trouble.
Don’t just repeat the same information, though. Change up the topic or present it in a different way. This will help keep employees focused and stop them from tuning out to a lesson they feel like they’ve heard several times before.
Likewise, use past sessions to fine-tune your training regimen. If you are tracking and recording results from each training, you will soon start to see gaps where important information isn’t getting across; those gaps can then be used as the basis for the next training session.
When it comes to training, never assume that your maintenance employees will fill in their knowledge gaps after a single training session. Everyone has different learning styles, and may require different strategies to learn effectively.
For more information to help you make the most of your plant’s maintenance efforts, download our free informative Ebook, Why and How to Cross-Train in Maintenance.